喷丸强化是以小的弹丸(铸钢丸、铸铁丸、陶瓷丸、玻璃丸等)为介质,通过控制大量弹丸高速且连续喷射,撞击零件表面,从而在表面产生残余压应力层,弹丸撞击零件表面时,就在其上撞出凹陷(或小压痕);凹陷形成时,金属表层产生拉伸,表层下压缩的晶粒试图将表面恢复到原来形状,就产生一个压缩力作用下的半球。无数的凹陷联接重叠,就形成了均匀的残余压应力层。最终,零件在表面压应力层的作用下,极大程度地改善其疲劳强度,从而延长了安全工作寿命。长期处于高应力工况下的金属零件,如飞机引擎压缩机叶片、机身结构件、汽车传动系统零件等,它们的制造工程中都要经过喷丸强化,以提高其抗疲劳需求[1]。钛合金因其比重小、比强度高、耐腐蚀性好等优点被广泛应用于航空航天等领域[2],但由于钛合金自身的疲劳强度低、分散性大、硬度和耐磨性较差等缺点限制了其进一步应用。喷丸强化是提高钛合金零件的抗疲劳性能和微动疲劳抗力的有效方法[3-4]。为研究喷丸参数对工件表面完整性参数的影响规律,国内外学者建立了不同的喷丸模型,进行了大量的仿真研究,文献[5-9]建立了不同的单弹丸撞击模型,包括四分之一模型、轴对称模型等,研究了不同喷丸参数对不同材料表面完整性参数的影响规律。在此基础上发展出了在空间按一定位置分布的阵列弹丸模型[10-13],通过控制弹丸的位置分布与数量来提高覆盖率。谢俊峰等[14]也对喷丸试验进行了研究。该喷丸试验中主要调整的喷丸参数包括喷丸直径、喷丸强度,通过调整这些喷丸工艺参数来研究喷丸强化后对18CrNiMo7-6渗碳齿轮表面性能的影响。总的来说,国内外对喷丸强化仿真进行了大量的研究,但研究靶材以钢材料为主,针对钛合金材料的喷丸仿真研究相对比较少,且建立的仿真模型以单丸模型为主,忽略了真实喷丸过程中弹丸位置的连续性和随机特性。因此,本文利用大型商业有限元软件Abaqus研究弹丸工艺参数对TC4钛合金喷丸强化影响规律,对喷丸冲击强化过程进行数值模拟,喷丸强化过程中主要调整的工艺参数为喷丸速度和弹丸入射角度。分别通过调整喷丸速度的大小和调整弹丸入射角度后对TC4钛合金靶材进行喷丸强化,得出对TC4钛合金喷丸强化的影响规律,对TC4喷丸工艺的制定具有重要的指导意义。
1、有限元模型建立
1.1 模型参数
在该多丸模型中弹丸采用直径为0.4mm的铸钢丸。为了方便建立之后的仿真模型,将TC4靶材的尺寸定义为2mm×2mm×1.5mm。为了使喷丸强化的效果达到和现实更接近,该模型中采用相对紧密的排列方式,如图1采用第n+1层相对于第n层向y轴偏移一定距离的方式分布。本文中采用的非对称模型都是使用25粒弹丸的喷丸强化模型。
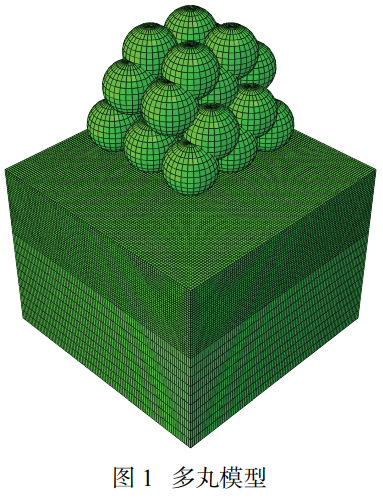
1.2 多丸模型网格划分
喷丸强化多丸模型的网格划分分为两个部分,靠近喷丸强化表面的部分尺寸为2mm×2mm×0.6mm,该部分在喷丸强化过程中产生主要的残余应力和塑性变形,为了保证模型计算结果的准确性和可靠性,将该部分设定为细化网格,该部分同样也是后处理过程中的主要分析区域,该部分细化网格共将该部分划分为300000个单元,细化单元的尺寸为0.02mm×0.02mm×0.02mm,在多丸模型中靶材和弹丸都选用C3D8R六面体线性减缩积分单元划分网格[15-16]。
1.3 多丸模型边界条件设置
通过对模型和实际情况的对比分析,在靶材模型仿真中,对底面约束了其法相位移和绕3个转轴的转动,对另外4个侧面仅约束了法向位移。该模型中设定相互作用为表面与表面接触,弹丸表面为第一接触面(主接触面),TC4靶材的上表面为第二接触面(从接触面),将弹丸设置为刚体,并且设置弹丸和靶材之间的摩擦因数为0.2。同样是对25粒弹丸设置初速度60m/s以模拟喷丸过程,先将该模型在Abaqus/Explicit中求解冲击过程,再将结果导入Abaqus/Standard中求解应力释放后的稳定收敛结果,得到喷丸强化后的残余应力分布。本文研究的是用铸钢丸作为弹丸材料对TC4钛合金靶材进行喷丸强化后的残余应力分析,两种材料的主要性能参数如表1所示。
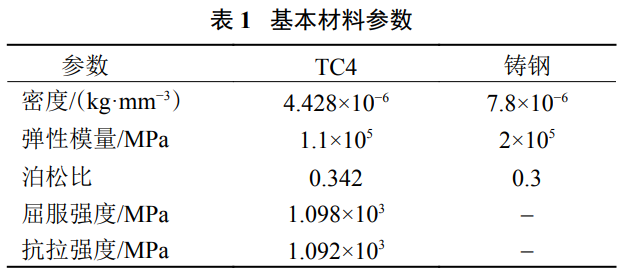
TC4的塑性应变参数如表2所示。

2、喷丸速度的影响
2.1 喷丸速度对残余应力的影响
本文建立的仿真模型中弹丸的直径为0.4mm,选取喷丸速度40m/s、60m/s、80m/s和100m/s分别进行分析。其喷丸模型的模拟结果如图2和图3所示。
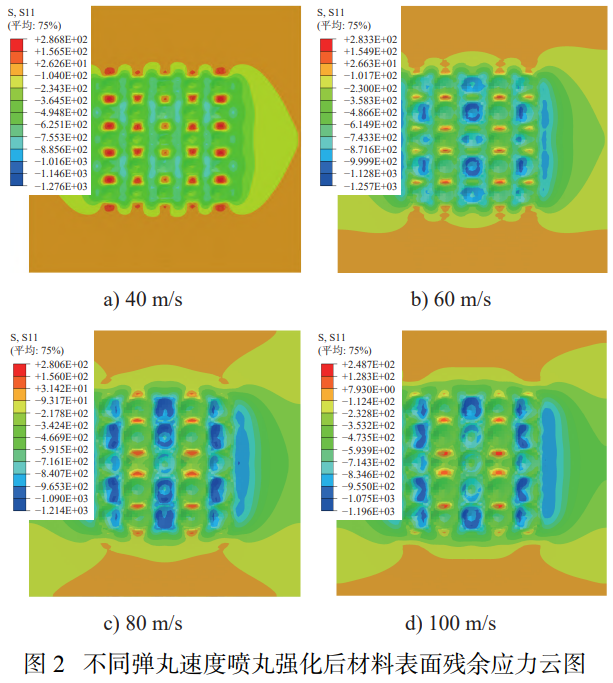
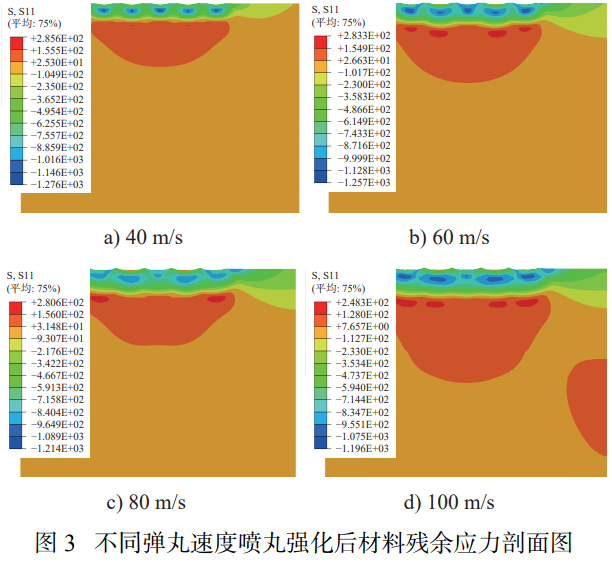
可以看出,弹丸速度较低时,喷丸后残余压应力主要集中在喷丸中心区域,随着喷丸速度的增加,残余压应力的范围逐渐扩大,在低速模型下的表面残余拉应力逐渐消失,因此不同的喷丸速度对靶材的残余应力情况有一定影响,喷丸速度越大,表面残余压应力越大,这主要归结于最表层材料发生了更大的塑性变形,而次表层的材料未能发生塑性变形,于是表层和次表层的材料发生相互作用而导致残余应力发生变化。
根据图3结果,TC4靶材在弹丸速度为40m/s的模型中喷丸强化后如图4所示,靶材表层形成了残余压应力层,随着厚度的增加,残余压应力减小,并且形成一定的残余拉应力。图4为TC4钛合金靶材在经过铸钢丸的不同弹丸速度喷丸强化后的表面残余应力的分布曲线。
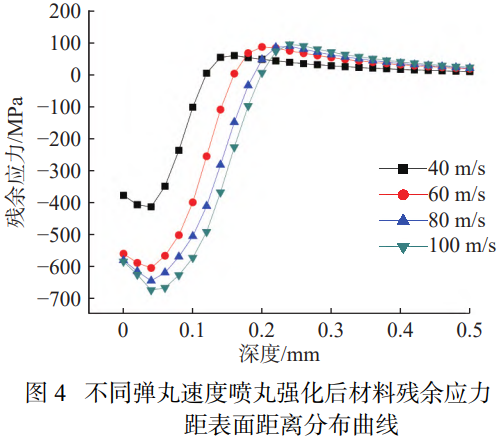
可以看出,喷丸速度由40m/s逐渐增大到100m/s,40m/s时表面残余压应力为379.8MPa,60m/s、80m/s和100m/s的表面残余应力都为587.2MPa左右,最大残余压应力由415.8MPa增加为669.1MPa,增幅37.8%,最大残余应力层距表面38.1μm增加到58.8μm。残余压应力层由118.7μm随弹丸速度的增加逐渐增加到198.6μm。可以得出随着弹丸速度的逐渐增加,弹丸携带的能量就越大,弹丸在撞击材料表面的过程中会使得材料发生更大的塑性变形,从而产生更大的残余压应力。在不考虑靶材表面粗糙度的情况下,喷丸强化过程中增大喷丸速度能够提高TC4钛合金的抗疲劳强度。
2.2 喷丸速度对表面粗糙度的影响
如图5所示,弹丸初速度40m/s、60m/s、80m/s和100m/s的喷丸强化后靶材表面节点沿Y方向(U2)的位移云图。
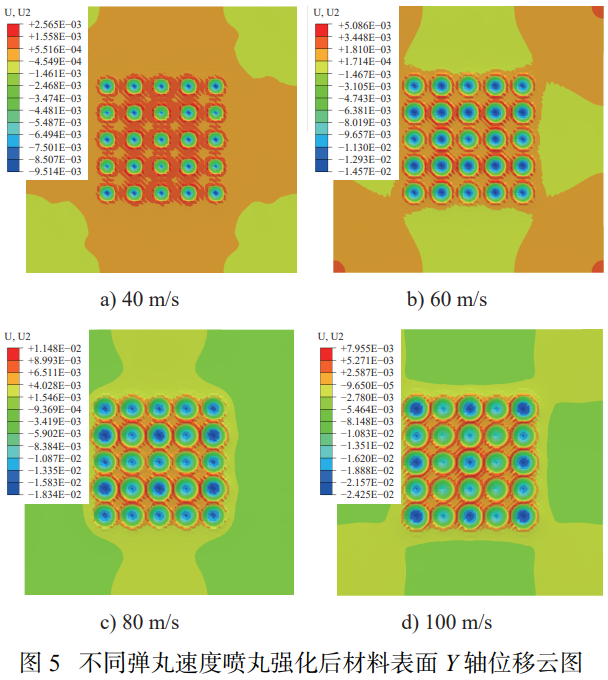
可以看出,在速度为40m/s的仿真模型中,弹丸在靶材表面的弹坑直径较小,在弹丸速度逐渐增大的过程中,弹坑直径也逐渐增大,通过运算得到不同弹丸速度喷丸强化后靶材表面的表面粗糙度。当弹丸速度为40m/s时,靶材表面的轮廓算术平均偏差为1.2μm,当弹丸速度为60m/s时,靶材表面的轮廓算术平均偏差为2.6μm,当弹丸速度为80m/s时,靶材表面的轮廓算术平均偏差为4.7μm,当弹丸速度为100m/s时,靶材表面的轮廓算术平均偏差为5μm。结果表明,喷丸速度越大,靶材表面粗糙度也越大,这一点其实很好理解,主要是由于弹丸速度过大在冲击材料表面时导致材料表面发生更大的塑性变形。表面粗糙度过大将导致过大的应力集中,这会影响到靶材的抗疲劳强度。综上所述,在喷丸过程中采用较高的速度能获得较大的表面残余压应力,最大残余压应力和残余压应力层厚度,对靶材抗疲劳强度的提升有显著效果,但是另一方面,过大的弹丸速度会降低靶材的表面完整性,从而对靶材的抗疲劳强度的提升具有副作用。因此,要共同考虑弹丸速度对残余压应力和表面粗糙度的影响,使喷丸对靶材的抗疲劳强度的提升达到最大。
3、入射角度的影响
3.1 入射角度对残余应力的影响
在上述两种分析方法中都是用垂直喷丸的方式,为了研究喷丸角度对喷丸效果的影响,分别建立了10°和20°喷丸入射角的模型,和垂直喷丸模型的结果进行对比。其喷丸模型的模拟结果X-Z方向的表面残余应力云图和X-Y方向的剖面残余应力云图如图6和图7所示,可以得出,在相同的弹丸速度和直径的情况下,改变弹丸的入射角度对靶材表面的弹坑大小没有显著的影响。
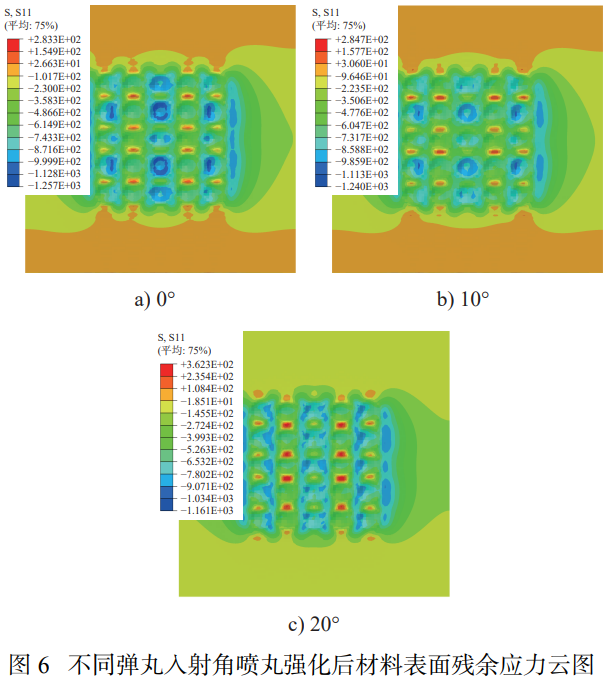
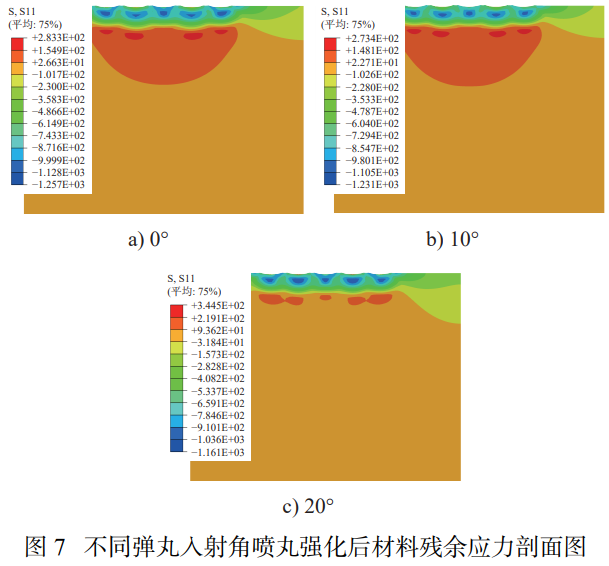
在各模型中选取模型中的节点分析残余应力,研究残余应力与距离表面距离的变化关系,得到如图8所示的3条残余应力分布曲线。分析图表数据可得,喷丸角度由垂直入射逐渐调整入射角为20°,表面残余压应力从562.4MPa减小为481.3MPa,最大残余压应力由607.3MPa逐渐减小为504.4MPa,降幅20.4%,最大残余应力层距表面基本没有变动。残余压应力层的厚度由158.5μm降低到145.2μm。可以得出喷丸的入射角度越大,速度和弹丸直径不变,则弹丸的能量不变,但是作用在Y方向的载荷分量逐渐变小,导致残余压应力层的厚度和最大残余压应力减小,在不考虑靶材表面完整性的情况下,弹丸入射角越小则喷丸强化更有利于提高靶材的抗疲劳强度。且同时可以从曲线图中分析得出,入射角为10°的情况相对于垂直入射对残余应力的影响并不大,但20°入射角相对与前两者残余应力下降的程度不能忽视,因此为了保证高质量的喷丸效果应尽量选择较小的入射角。
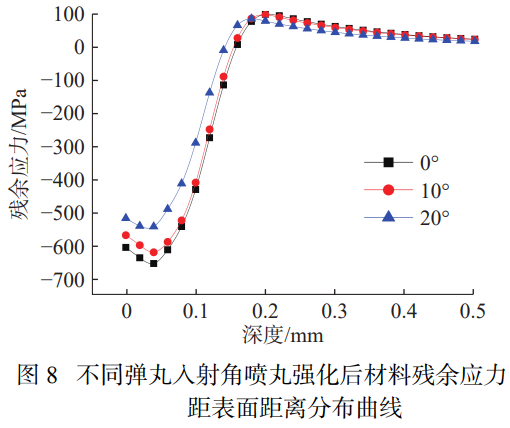
3.2 入射角度对表面粗糙度的影响
如图9所示,垂直入射、入射角为10°和入射角为20°的喷丸强化后靶材表面节点沿Y方向(U2)的位移云图,通过运算得到不同入射角度喷丸强化后靶材表面的轮廓算术平均偏差,当弹丸垂直入射时,靶材表面的轮廓算术平均偏差为2.6μm,当弹丸入射角为10°时,靶材表面的轮廓算术平均偏差为2.57μm,当弹丸入射角度为20°时,靶材表面的轮廓算术平均偏差为2.56μm。结果表明,随着弹丸入射角度的增加,靶材表面粗糙度会稍有降低,但其变化幅度较小,对表面完整性的影响不显著。
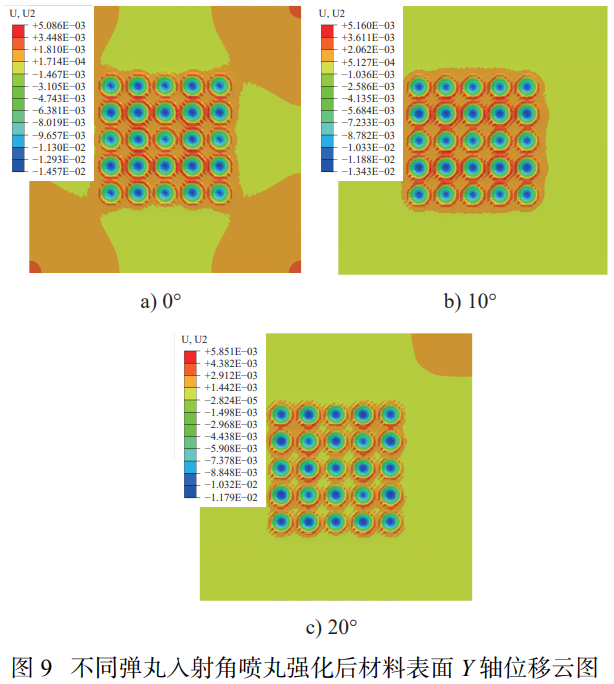
综上所述,随着入射角的不断增大,靶材的表面粗糙度并没有显著的改变,但对残余压应力的影响不可忽视,同时考虑到现实喷丸强化过程中,垂直喷丸时,反弹的弹丸和入射的弹丸之间产生碰撞导致能量损失,进而会大幅影响喷丸效果,则不宜选用垂直的喷丸方式。因此,应该选择具有一定入射角的喷丸方式,同时为了使喷丸强度和喷丸效果达到最优,入射角度控制在0~10°之间最合适。
4、结论
为了研究工艺参数对TC4钛合金喷丸强化的影响效果,运用Abaqus模拟软件建立了TC4钛合金喷丸强化的有限元仿真模型,运用该模型分别对弹丸初速度分别为40m/s、60m/s、80m/s和100m/s的模型和弹丸入射角度分别为垂直入射、入射角为10°和入射角为20°的TC4钛合金进行了喷丸强化仿真分析,最终得到结论如下:
1)TC4钛合金经过喷丸强化后,表面沿深度方向会依次形成残余压应力层和残余拉应力层,残余压应力层对钛合金的力学性能提升有显著作用,但最大残余应力出现在次表层。
2)当喷丸速度逐渐增大的过程中,表面残余应力,最大残余压应力和残余压应力层厚度都逐渐增大,靶材的表面粗糙度由1.2μm增加到5μm。
3)随着入射角的不断增大,靶材的表面粗糙度并没有显著的改变,但对残余压应力的影响不可忽视,主要体现在最大残余应力由607.3MPa逐渐减小为504.4MPa,降幅20.4%,残余压应力层的厚度由158.5μm降低到145.2μm,降幅8.4%。为了使喷丸强度和喷丸效果达到最优,入射角度要控制在0~10°之间最合适。
[ 参考文献 ]
[1]机械工程名词审定委员会. 机械工程名词[M]. 北京:
科学出版社, 2003 National Scientific and Technical Terms Review Committee. Mechanical engineering terms[M]. Beijing: Science Press, 2003 (in Chinese)
[3]孟龙晖. Ti6Al4V钛合金切削加工表面残余应力的研 究[D]. 南京: 南京航空航天大学, 2016
MENG L H. Research on surface residual stresses generated by machining Ti6Al4V titanium alloy[D]. Nanjing: Nanjing University of Aeronautics and Astronautics, 2016 (in Chinese)
[3]季秀升, 李小强, 邓同生. TA15钛合金喷丸强化[J].塑性工程学报, 2012, 19(3): 76-78
JI X S, LI X Q, DENG T S. Study on shot peening of TA15 titanium alloy[J]. Journal of Plasticity Engineering, 2012, 19(3): 76-78 (in Chinese)
[4]冯宝香, 杨冠军, 毛小南, 等. 钛及钛合金喷丸强化研 究进展[J]. 钛工业进展, 2008, 25(3):1-5 FENG B X, YANG G J, MAO X N, et al. Research development of shot peening strengthening of titanium alloys[J]. Titanium Industry Progress, 2008, 25(3): 1-5(in Chinese)
[5]王延忠, 李菲, 陈燕燕, 等. TC4喷丸强化仿真与试验[J].北京航空航天大学学报, 2019, 45(9):1723-1731
WANG Y Z, LI F, CHEN Y Y, et al. TC4 shot peening simulation and experiment[J]. Journal of Beijing University of Aeronautics and Astronautics, 2019, 45(9): 1723-1731 (in Chinese)
[6]WANG C, LAI Y B, WANG L, et al. Dislocation-based study on the influences of shot peening on fatigue resistance[J]. Surface and Coatings Technology, 2020, 383: 125247
[7]HUANG H M, WANG Z, GAN J, et al. The study of universality of a method for predicting surface nanocrystallization after high energy shot peening based on finite element analysis[J]. Surface and Coatings Technology, 2019, 358: 617-627
[8]KHAJEIAN A, MAHMOUDI A H, MEHMANPARAST A. Shot peening effects on residual stresses redistribution of offshore wind monopile multi-pass weldments[J]. Marine Structures, 2019, 66: 106-120
[9]HONG T, OOI J Y, SHAW B A. A numerical study of the residual stress pattern from single shot impacting on a metallic component[J]. Advances in Engineering Software, 2008, 39(9): 743-756
[10]ZHANG Y L, LAI F Q, QU S G, et al. Effect of shot peening on residual stress distribution and tribologicalbehaviors of 17Cr2Ni2MoVNb steel[J]. Surface and Coatings Technology, 2020, 386: 125497
[11]MANCHOUL S, SEDDIK R, SGHAEIR R B, et al. Finite element modeling of ultrasonic and conventional shot peening: a comparison of the effect of both processes on surface conditions[J]. Proceedings of the Institution of Mechanical Engineers, Part L:Journal of Materials:Design and Applications, 2019, 233(5): 930- 941
[12]FAKSA L, DAVES W, KLÜNSNER T, et al. Shot peening-induced plastic deformation of individual phases within a coated WC-Co hard metal composite material including stress-strain curves for WC as a function of temperature[J]. Surface and Coatings Technology, 2019, 380: 125026
[13]WANG C, WANG L, WANG X G, et al. Numerical study of grain refinement induced by severe shot peening[J]. International Journal of Mechanical Sciences, 2018, 146-147:280-294
[14]谢俊峰, 何声馨, 李纪强, 等. 喷丸强化对18CrNiMo7-6渗 碳 齿 轮 表 面 性 能 的 影 [J]. 热 加工 工 艺 , 2017, 46(18): 179-181,186
XIE J F, HE S X, LI J Q, et al. Effect of shot peening on properties of 18CrNiMo7-6 carburizing gear surface[J]. Hot Working Technology, 2017, 46(18): 179-181,186 (in Chinese)
[15]庄茁, 由小川, 廖剑晖, 等. 基于ABAQUS的有限元分 析和应用[M]. 北京: 清华大学出版社, 2009: 56-62
ZHUANG Z, YOU X C, LIAO J H, et al. Finite element analysis and application based on ABAQUS[M]. Beijing: Tsinghua University Press, 2009: 56-62 (in Chinese)
[16]曹金凤, 石亦平. ABAQUS有限元分析常见问题解 答[M]. 北京: 机械工业出版社, 2009: 92-97
CAO JF, SHI Y P. Frequently asked questions about ABAQUS finite element analysis[M].Beijing: Mechanical Industry Press, 2009: 92-97 (in Chinese)
相关链接