本文通过对某左中接头锻件结构特点及该锻件在低倍中出现的模糊晶和抗拉强度略低于标准值的情况查找原因进行分析。结合锻件特点对荒形工步进行了改进,并增加了预锻模,降低了每工步变形量。最终解决了锻件低倍模糊晶和抗拉强度低的问题,从而反映了变形量大对大规模锻件的影响,为后续大规模锻件生产提供了一些帮助。
左中接头锻件(图1)是某民用飞机的大型钛合金锻件,长3m 左右,材料为Ti-6Al-4V,为TIMET料,因其锻件比较大,模锻过程中发现产品垂直尺寸超正差,在理化试验过程中被发现低倍试样中存在模糊晶等问题。在8 号产品的流线较明显处取样,取低倍处厚度为129mm,共计3个,在某外厂做拉伸试验。发现屈服强度略高于标准要求,但是数值略低,抗拉强度低于标准数值。当发现此问题后我们对所交付的产品进行了复查。复查原材料、工艺文件、生产过程、锻件出厂检验结果,工艺文件符合此客户锻件图和标准要求;原材料复验结果符合此客户标准,制坯、模锻、热处理等生产过程符合工艺规程要求;首批解剖件和100%理化试料出厂检验结果符合标准CMS-Ti-203 D 要求。经过对工艺和图纸的反复讨论,我们发现有可能是荒形设计工步较少,没有预锻设计造成的。经过改进工艺,增加预锻模解决了此问题,具体讨论如下文所示。
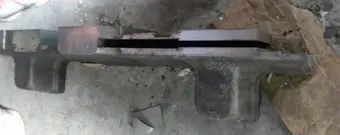
图1 左中接头锻件
发现锻件低倍流线和模糊晶
⑴高、低倍组织检查结果(图2)。模糊晶界处同一位置不同放大倍数下的低倍组织(图3),因A,B,C 三处模糊晶低倍组织相似,选用A 的低倍组织图用于此文章的分析和讨论。
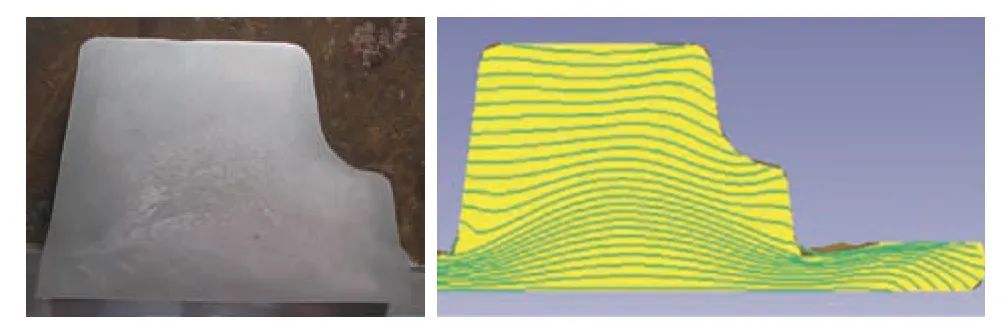
图2 低倍流线与模拟流线
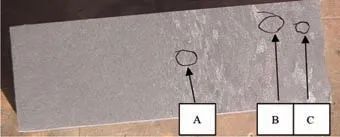
图3 模糊晶界处同一位置不同放大倍数下的低倍组织
⑵力学性能试验。
为了验证低倍试样中模糊晶的晶粒形态呈流线形式分布对力学性能的影响,在流线较明显处取样A、B、C,连同无流线明显处取样D、E、F,共六处在外厂做拉伸试验。试验结果见表1,对比图如图4、图5 所示。
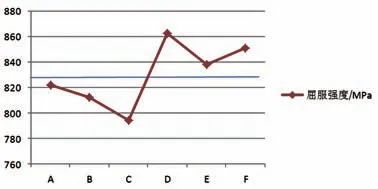
图4 模糊晶屈服强度与正常晶粒对比图(横线以上为标准范围)
表1 模糊晶和正常晶粒组织对比试验
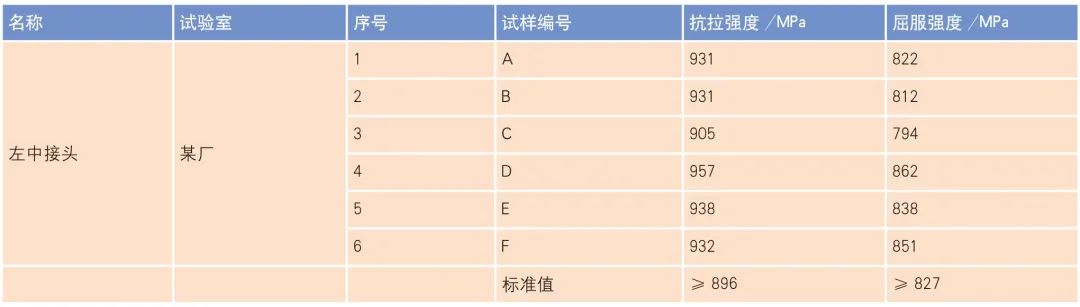
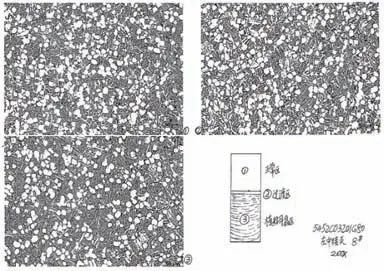
图5 模糊晶与正常晶粒对比图
通过数据对比发现模糊晶的抗拉强度虽符合标准值的要求,但仅仅是稍高于标准值,屈服强度略低于标准要求。
原因分析
此锻件为大型钛合金锻件,在最初设计锻荒时,设计工步较少,造成每工步变形量大,有可能造成了产品在生产过程中出现模糊晶。再者此锻件有几件产品发现垂直尺寸超正差,应该是由于未增加预锻工序,导致锻荒后产品尺寸未调整到统一尺寸。此锻件仅做退火处理暂不考虑退火引起模糊晶。
改进措施
⑴在原有工艺规程的基础上,细化每火次变形量,合理制定每火次后的荒形尺寸。(原来荒形仅有三工步,每工步变形量大于50%)
⑵制荒坯过程中,严格按照工艺要求尺寸,使坯料在每火次后尺寸一致较好。
⑶制坯过程打击力量(压下量)做到量化,尽量减小件与件之间的差异。
⑷在制坯完成后增加预锻成形,从根本上解决模锻前荒形一致性的问题。(由原来的3 工步增加的5工步,前三工步变形量减少到40%以下,后面三工步变形量减少到25%以下,变形量减少使变形均匀。)
荒形改进后,产品所做高低倍组织均未见异常,无模糊晶。高低倍照片如图6 所示。
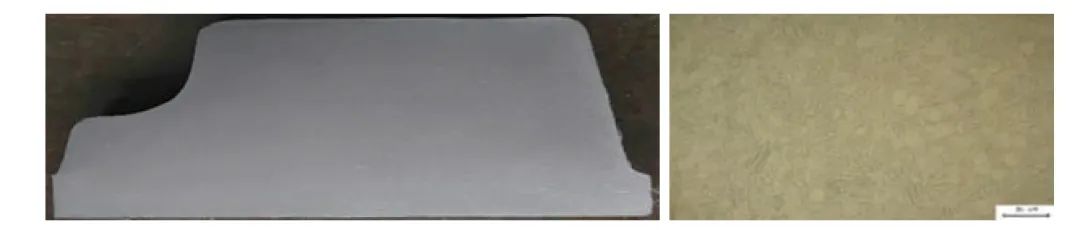
图6 荒形改进后产品高低倍照片
结论
本文所探讨的左中接头锻件为大型钛合金锻件,通过对锻荒工步的细化改进和增加,减少了产品每工步的变形量,使产品的每一步锻荒和模锻都在可控范围内。在制坯完成后增加的预锻成形工序,从根本上解决模锻前荒形一致性的问题。减少了产品缺陷,设计方案科学合理,利于锻造出良好的产品,更适合于实际生产。
——文章选自《锻造与冲压》2023年第7期
相关链接