引言
钛及钛合金具有抗腐蚀性能、比强度高、磁导率低等优秀性能,钛无缝管材被较多地应用于飞机管路系统、化工用传输管道和船舶用热交换器管等特种行业。近年来,也逐步被应用于发电站用冷凝器、石油开采用钻杆和海水淡化用加热器等高附加值民用领域,市场前景广阔。经过统计,2021年全球钛无缝管市场规模超过了20亿元,预计2027年将达到29亿元。
钛从矿石中提取比较困难,且传统无缝管制备工艺复杂、成本高昂,这限制了钛及钛合金无缝管在市场上得到更广泛的应用。由于成本的限制,目前国内外很多民品行业依然选用传统的不锈钢管或者钛焊接管,而不是性能更为优秀的钛及钛合金无缝管。
现阶段,除钛及钛合金无缝管材制备主要参照不锈钢管行业的设备和加工工艺进行加工,工艺成熟度高,改进空间小,无法有效缩短加工周期和降低加工成本。为了降本增效,本文决定从源头上进行改进,规避了传统的熔炼、锻造、穿孔等工序,进行了全流程的工艺创新和优化。新工艺依次通过熔炼铸态空心管坯、径向锻造、双重退火和机加工流程,得到钛合金管材,缩短加工周期的同时,有效降低了生产成本。
1、国内无缝管制备技术现状
传统钛合金无缝管制备工艺首先经过熔炼生产柱状钛合金锭,并采用热锻工艺制备棒材,每火次均需要加热、保温、变形和扒皮。棒坯加工完成后,后续再采用斜轧穿孔、热挤法等方法制备管坯。最后配以热轧、冷轧、机加工等辅助工艺制备成品无缝管,如图1所示。
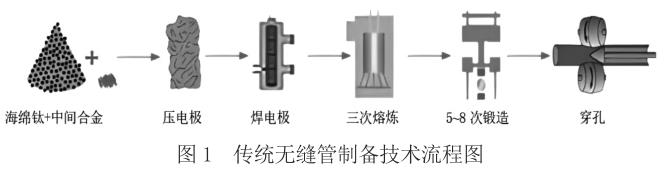
棒坯制备工艺生产能耗大,生产周期长,原材料生产损耗大,成材率低;使用热挤法穿孔制备管坯时,由于挤压法最终需要留出料头,导致材料利用率偏低,工艺流程长,且钛合金变形抗力大,需要较大吨位挤压设备,也限制了钛合金无缝管的生产。使用斜轧穿孔工艺制备管坯,这种工艺加工周期短,但是由于加工时温度高,所以得到的产品组织差,大多数为网篮组织或者魏氏组织,且设备占地面积大,能耗高。
2、新型无缝管制备技术
为解决上述技术问题,以快速高效生产低成本的高强高韧钛合金无缝管材,本文现提出一种钛及钛合金管材的短流程制备方法[1],包括:铸钛管坯生产、径向锻造、双重退火和机加工流程,得到钛合金管材,如图2。具体表现为直接利用等离子枪或者电子束枪融化原材料生产空心管坯,然后通过径向锻造改良管坯的组织,再利用双重退火均匀组织和消除径向锻造的内应力,最后采用机加工保证成品管的表面质量和尺寸。直接熔炼生产管坯除了缩短工艺,同时可以有效去除高低密度夹杂,得到纯洁度更高的产品。区别于传统的锻造,径向锻造可以直接对管坯进行锻造,提高加工效率和材料利用率。双重退火首先通过高温促进产品再结晶,然后进行低温处理均匀化组织的同时消除内应力。
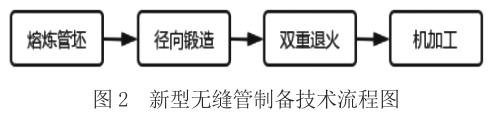
3、加工工艺
3.1铸态管坯制备
使用等离子枪或者电子束枪直接对海绵钛和中间合金混合物进行熔炼,避免了烦琐的钛合金压电极、焊电极和真空熔炼工序的同时,直接熔炼出高纯净度的管状空心铸锭,如图3。也可以将传统柱状钛合金铸锭经过钻孔工艺得到管坯,然后将钛屑回收重熔。
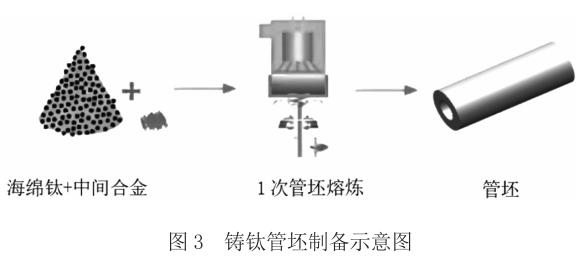
3.2径向锻造
将铸态管坯加热至钛合金β相变点以上,再进行三次径向锻造,然后经过双重热处理,最后得到成品管坯,如图4。区别于传统的锻造,径向锻造可以直接对管坯进行锻造,提高加工效率和材料利用率的同时,通过大量变形使得管坯的铸态晶粒被充分破坏,再使用高速锤击,使得晶粒得到细化,从而使得管坯的致密性、连续性以及力学性能得到提高,得到优秀的组织。
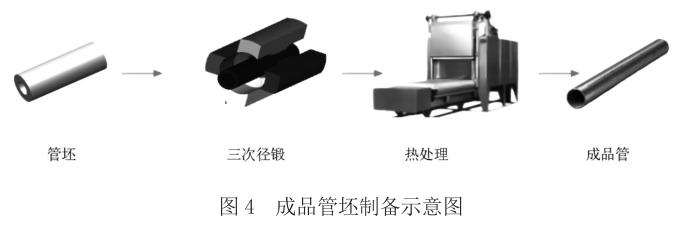
径向锻造前,管坯中间插入芯棒,并装夹到径向锻造机上,且第一夹头夹持在管坯的一端,锤头位于管坯的另一端,第二夹头夹持在与锤头同一端的芯棒上;三次锻造前,均需更换芯棒,所述芯棒的直径比装夹的管坯的内径小15~20mm,如图5。
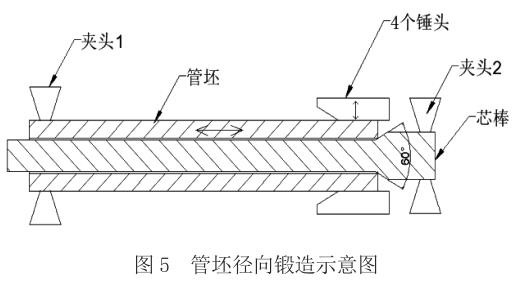
加热温度在钛合金β相变点以上80~100℃,保温时间≥2h;多次径向锻造包括三次径向锻造。
第一次径向锻造中,采用四个平面锤头,并控制管坯沿中心轴方向移动[2],移动的速度为1~3m/min,锤击速度为1000~2000n/min,管坯变形量控制在40%~80%。第一次径向锻造后,得到的管坯,其截面呈外正方形内圆形的形状,如图6。
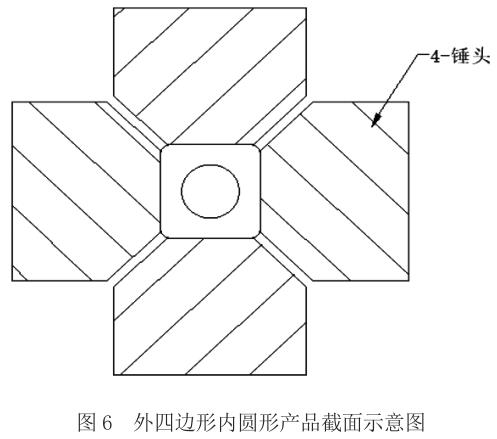
第二次径向锻造中,采用四个平面锤头,控制管坯绕自身轴向旋转40~50°后,开始锻造,并使管坯沿中心轴方向移动,移动的速度为3~5m/min,锤击速度为2000~3000n/min,管坯变形量控制在30%~60%。第二次径向锻造后,得到的管坯,其截面呈外八边形内圆形的形状,如图7。
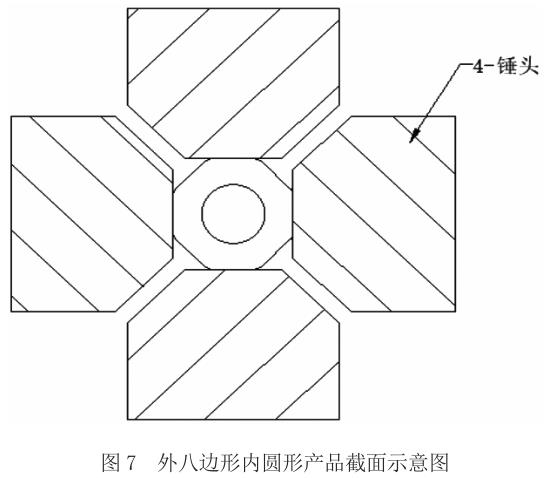
第三次径向锻造前,均需更换芯棒,所述芯棒的直径比装夹的管坯的内径小15~20mm。锻造时,采用四个曲面锤头,所述曲面锤头的曲面直径比管坯的外径大80~120mm。待工件温度降低到钛合金β相变点以下40~60℃,并控制管坯进行自转及沿中心轴方向移动,自转转速为300~600rpm,移动的速度为3~5m/min,锤击速度为50~100n/min,管坯变形量控制在30%~40%。第三次径向锻造后,产品恢复为圆形管坯,钛合金管材的总体形变量≥100%。
将管坯加热至钛合金β相变点以上80~100℃,再进行三次径向锻造,经过高速锤击,使管坯的温度升高,从而减小变形抗力,但同时不会出现温度过热烧坏工件的情况[3];且在三次锻造的过程中,管坯的外管在锻造中,由圆形锻造成正方形,再由正方形锻造成八边形,最后由八边形再锻造回圆形,使得管坯的铸态晶粒被充分破坏,再经过高速锤击,加大管坯的变形量,使得晶粒得到细化,从而使得管坯的致密性、连续性以及力学性能得到提高,力学性能提高15%以上,且直接得到等轴或双态组织。
3.3双重退火
将径向锻造后的锻态管坯进行双重退火,通过高温促进组织的再结晶,消除锻造变形的影响,再利用低温处理,消除热应力的同时,进一步均匀组织。具体工艺如下:先将经过多次径向锻造后的钛合金管加热到850~930℃,并保温0.5~5h后空冷至室温;再次加热到450~550℃。并保温0.5~5h后空冷至室温,消除管材内应力。
3.4机械加工
将退火态钛合金管进行机械加工,以达到尺寸、表面粗糙度的精度要求,得到所需的钛合金管材。
4、样件试制
通过上文所述短流程生产工艺生产ODФ200*IDФ150mm规格的TC4钛合金无缝管[4]。
S1:准备ODФ520mm*IDФ200mm的铸态钛合金管材坯料。
S2:将管坯表面涂抹防氧化涂层,加热到1070℃,并保温6h。
S3:将管坯料装夹到径向锻造机上,第一夹头夹持管坯。另准备Ф180mm芯棒一根,插入管坯内,锤头在管坯的另一端,且该端的芯棒具有60°的锥度,第二夹头夹持在与锤头同一端的芯棒上。
S4:第一次径向锻造,管坯变形量60%,四个锤头作径向往复式运动,锤击速度1500n/min,第一夹头和第二夹头控制管坯和芯棒沿中心轴方向移动,移动的速度为2m/min,得到截面为外正方形内圆形的管坯。
S5:第二次径向锻造,更换芯棒,芯棒尺寸为Ф160mm,芯棒和管坯的夹持方式与步骤S3相同,管坯绕自身轴向旋转45°后开始锻造,管坯变形量在60%,四个锤头作径向往复式运动,锤击速度2500n/min,第一夹头和第二夹头控制管坯和芯棒沿中心轴方向移动,移动的速度为4m/min,得到截面为外八边形内圆形的管坯。
S6:更换芯棒,芯棒尺寸为Ф140mm,芯棒和管坯的夹持方式与步骤S3相同,等工件温度空冷到930℃开始第三次径向锻造,管坯变形量在40%,四个锤头作径向往复式运动,锤击速度70n/min,第一夹头和第二夹头控制管坯和芯棒进行自转及沿中心轴方向移动,自转转速550rpm,移动的速度为4m/min,管坯尺寸变为ODФ210mm*IDФ140mm。
第三次径向锻造后,管坯的总变形量为160%。
其中曲面锤头的曲面直径为360mm。
S7:将S6所得的无缝管材进行双重退火,双重退火首先加热到900℃,保温3h后空冷至室温,再次加热到500℃保温3h后空冷至室温,使亚稳相全部分解,管材内应力完全消除。
S8:将S7所得双重退火态钛合金管进行车削加工,使管材直径加工至ODФ200mm*IDФ150mm,得到优良组织的钛合金无缝成品管。
利用上述短流程工艺制备的钛合金无缝管材,从铸锭到成品管,总共花费的时间不到16h,成本约120元/kg,加工周期短,成本低[5]。
对上述钛合金管材进行性能测试,其金相测试结果显示,组织形态为等轴(图8)或双态组织(图9);其抗拉强度为900~950MPa,屈服强度880~920MPa,断后
收缩率20%,断后延伸率40%。
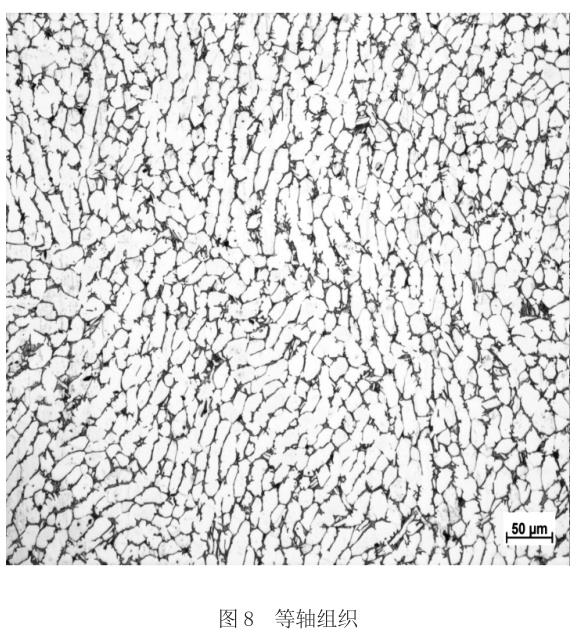
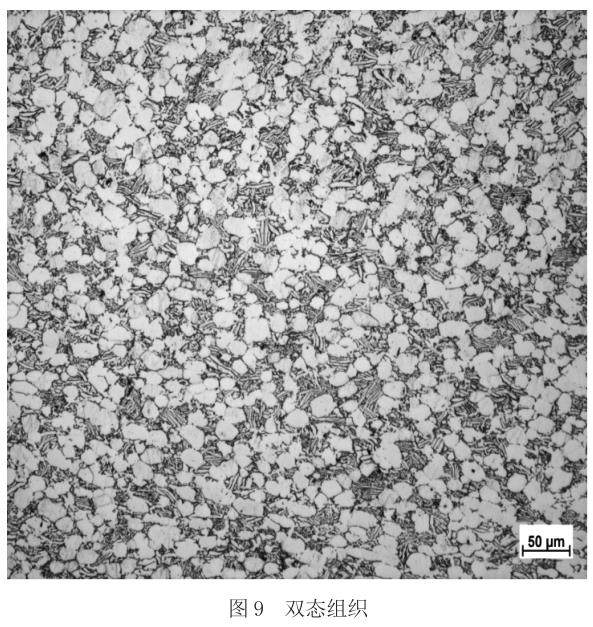
5、结论
综上所述,本文所述的高强高韧钛合金无缝管材制备技术,从管坯加热工序开始,加热温度低,保温时间短,且直接经过三次径向锻造就可以直接得到具有优良组织以及优异
力学性能的钛合金管材,一体成型,材料利用率高,且整个工艺加工周期短、能耗低,从而降低了成本,更有利于工业化生产,可以用于高强高韧钛合金无缝管材的批量生产。
【参考文献】
[1]王长江.一种低成本钛合金薄壁管材的制备方法[J].信息记录材料,2022,23(4):58-61.
[2]车永平,田宇兴,张亚峰,等.近β型TLM钛合金细径薄壁管材力学行为研究[J].稀有金属材料与工程,2016,45(4):923-927.
[3]董恩涛.高强α+β钛合金无缝管热轧工艺及组织性能调控研究[D].北京:北京科技大学,2022.
[4]庞玉华,何威威,刘东,等.TC4钛合金锥形辊斜轧穿孔曼内斯曼效应[J].塑性工程学报,2020,27(3):109-114.
[5]吴捍疆,张丰收,燕根鹏.基于数值模拟的TC4钛合金航空叶片精锻过程的金属流动规律[J].锻压技术,2020,45(2):7-14.
作者简介:王长江(1985—),男,江苏无锡,本科,工程师,研究方向:钛及钛合金制备技术和设备。
相关链接