钛合金具有高的比强度、比刚度、无磁性和良好的耐腐蚀性能,可以满足轻量化、高机动性、高可靠性和长寿命的设计要求,在航空航天、兵器装备等领域得到广泛应用[1-3]。中国第五代战机歼20的用钛量达到了20%,而美国的F-35和F-22分别达到了27%和41%,其中发动机的叶轮、盘、叶片、机匣、燃烧室等部件均采用钛合金制造[4-5]。民用航空方面,美国波音787用钛量达到15%,而中国自主研发的干线客机C919用钛量达到机身结构重量的9.3%,远超同级别波音737的4%和空客A320
的4.5%。美军的M1“艾布拉姆斯”主战坦克、M2“布雷德利”步兵战车以及“斯特赖克”轮式装甲车、法国陆军新型步兵战车(VBCI)、俄罗斯T-90A和T-95主战坦克、英国改进型“武士”步兵战车等装甲车辆实现了钛合金的规模化应用,均取得了明显的减重和防护效果[6-7]。
增材制造(additivemanufacturing,AM)技术自20世纪发展以来备受关注,在航空航天等领域展现出独特价值和广阔的应用前景,使得航空航天构件向智能化制造发展,被列入决定未来经济的十二大颠覆性技术之一[8-9]。钛合金具有热传导率低、加工硬化、弹性模量低等特性,使得构件加工困难,材料利用率低,加工制造周期长、成本高。基于金属粉末材料的增材制造技术,如激光选区熔化成形(selectivelasermelting,SLM)和电子束选区熔融成形(electronbeamselectivemelting,EBM)可适用于多品种、小批量、复杂形状零件的生产。
而激光立体成形技术(lasersolidforming,LSF)可适用于大型构件的成形、修复和再制造,目前已初步形成市场规模[10-11]。与金属粉末材料相比,金属丝材增材制造技术具有沉积效率高、成本低、材料利用率高、交付周期短的显著优势[12]。目前,基于丝材的金属增材制造技术根据热源类型的不同,主要有电弧熔丝增材制造技术(wirearcadditivemanufacturing,WAAM)、电子束熔丝沉积成形技术(electronbeamfreeformfabri⁃cation,EBF3或EBAM)、激光熔丝增材制造技术(laser
andwireadditivemanufacturing,LWAM)等。
本文以钛合金丝材为原材料,探讨了电弧熔丝、电子束熔丝和激光熔丝增材制造技术,针对成形工艺、宏微观组织结构及应用场景存在的问题,从新型工艺优化、组织性能调控及原材料开发等方面进行了综合论述。同时,对基于钛合金丝材的增材制造技术存在的关键技术问题进行探讨,指明了未来的主要研究及应用方向。
1、电弧熔丝增材制造技术
电弧熔丝增材制造技术于1926年被提出,随着工业自动化、数字化技术的发展,这一技术越来越受到工业界的青睐[13]。与传统的减材制造相比,电弧熔丝增材制造可缩短40%~60%的制造周期,后续机加工时间可缩短15%~20%,同时可节约78%左右的原材料成本[14-15],可替代传统的钛合金铸造和锻造技术,从而实现钛合金构件的低成本制造。
1.1组织与性能优化
电弧熔丝增材制造的钛合金构件均存在粗大的外延生长β柱状晶、条带组织和魏氏组织,不同区域的显微组织不同,导致不同区域、不同方向的力学性能差异较大。上海交通大学林建军[16]通过Ti-6Al-4V合金的脉冲等离子弧熔丝增材制造(pulsedplasmaarcadditivemanufacturing,PPAM),发现宏观组织主要由粗大的初生β晶粒和层束组织构成,显微组织主要由马氏体α'和具有网篮特征的魏氏组织构成,如图1所示。基于普通的WAAM工艺,研究人员开发出热双丝电弧增材制造技术(double-hot-wireandarcadditivemanufactur⁃ing,DHWAAM),该技术具有较低的热输入和接近双倍的沉积效率,沉积态宏观上接近等轴晶,呈典型的网篮组织[17-18]。在该工艺基础上,进一步采用图2所示的层间冷却和连续沉积两种策略,优化沉积层数(N)和层间冷却时间(t),发现层间冷却后,粗大柱状晶转变为等轴晶和细小的柱状晶,晶界连续α相和α集束组织均减少,构件的室温力学性能优于连续沉积,如图3和图4所示。
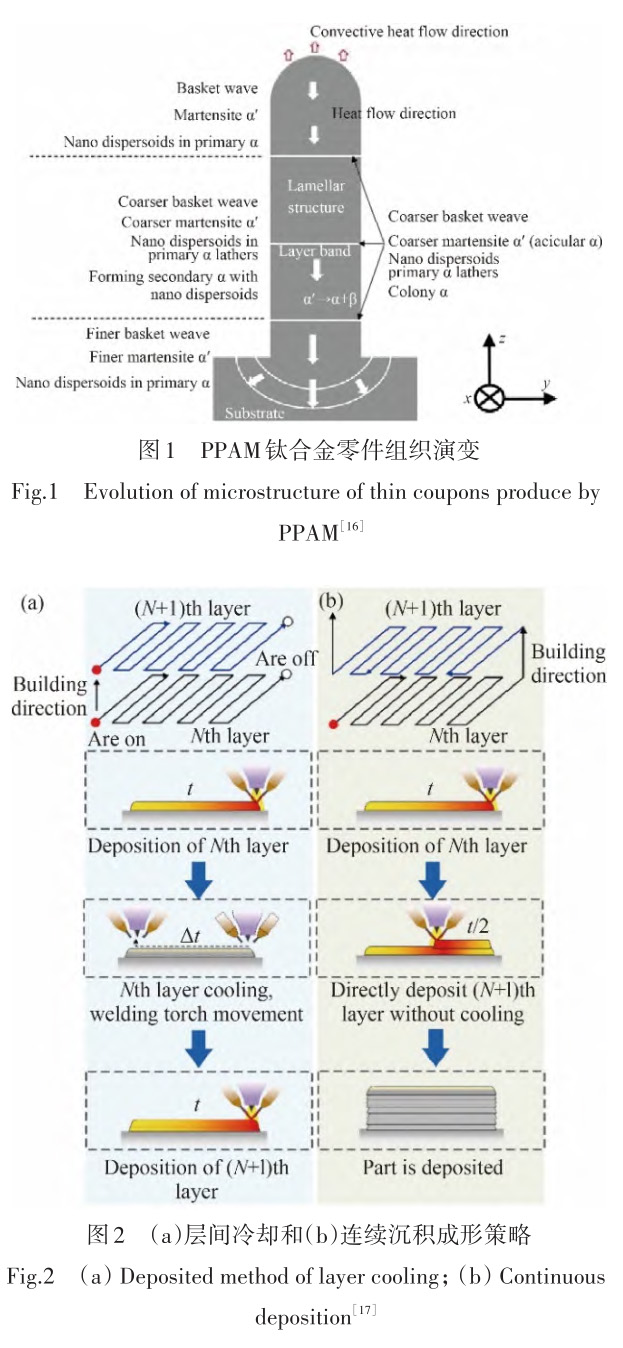
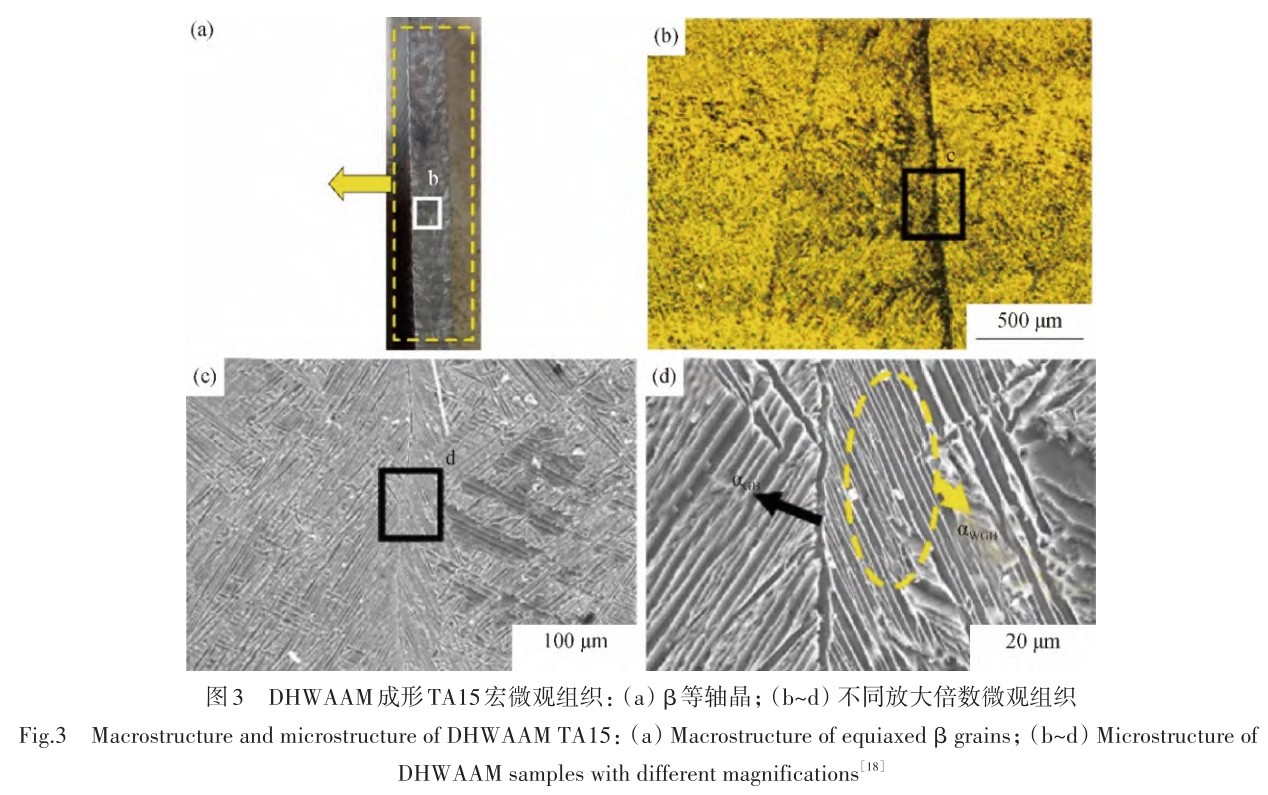
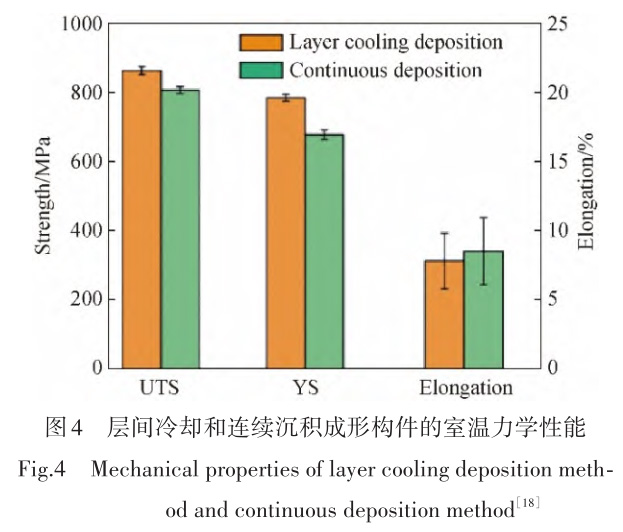
通过WAAM工艺的优化,虽然可以获得部分初生等轴晶组织,但各向异性依然明显,研究人员尝试对处于高温的沉积金属进行形变处理,力求实现晶粒细化。McAndrew等[19]和Hönnige等[20]对WAAM成形Ti-6Al-4V合金进行层间辊压和锤击,使初生β晶粒破碎,产生新的取向,促使晶粒细化。其次,通过图5所示的原位微轧制+电弧熔丝混合制造技术(hybridinsiturolledwire+arcaddi⁃tivemanufacturing,HRAM)[21],使Ti-6Al-4V合金的沉积层发生塑性变形和动态再结晶,促进形成更
宽的α板条,约为WAAM的两倍,WAAM和HRAM成形的Ti-6Al-4V合金中α板条的平均尺寸如图6所示,其力学性能见表1,可见HRAM工艺明显优于WAAM工艺
[21]。随后进行准β热处理,初生β晶粒和α片层组织更为细小,图7为WAAM和HRAM成形的TC4-DT合金断裂机理示意图,可以明显看出受HRAW成形组织的影响,扩展过程中出现二次裂纹,扩展速率明显低于WAAM[22]。其次,利用激光冲击(lasershockpeening,LSP)和超声冲击,改善WAAM成形组织和性能。激光冲击使钛合金表面产生剧烈塑性变形,表层组织发生孪晶变形,产生大量位错,初生α相和次生α相明显细化,构件表层引入压应力,表面硬度提升HV50,如图8所示
[23]。超声冲击则使WAAM成形钛合金沉积层的位错发生增殖和迁移,造成晶粒破碎,同时增多了形核质点,粗大的柱状晶转变为细小的等轴晶,微观组织和力学性能的各向异性明显减小[24]。
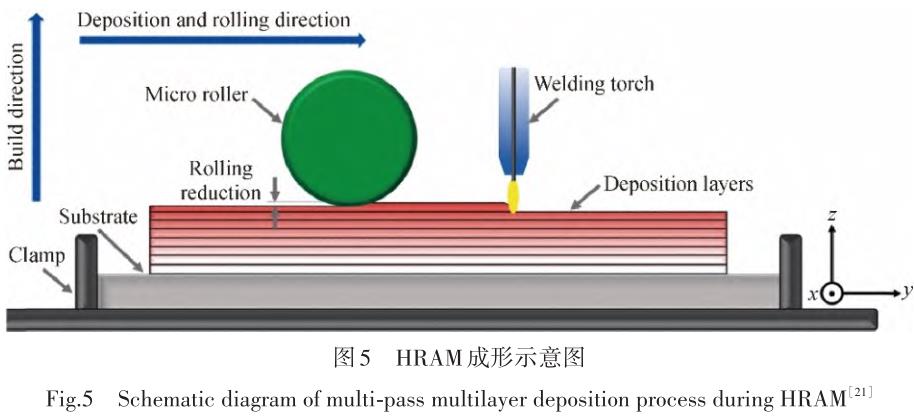
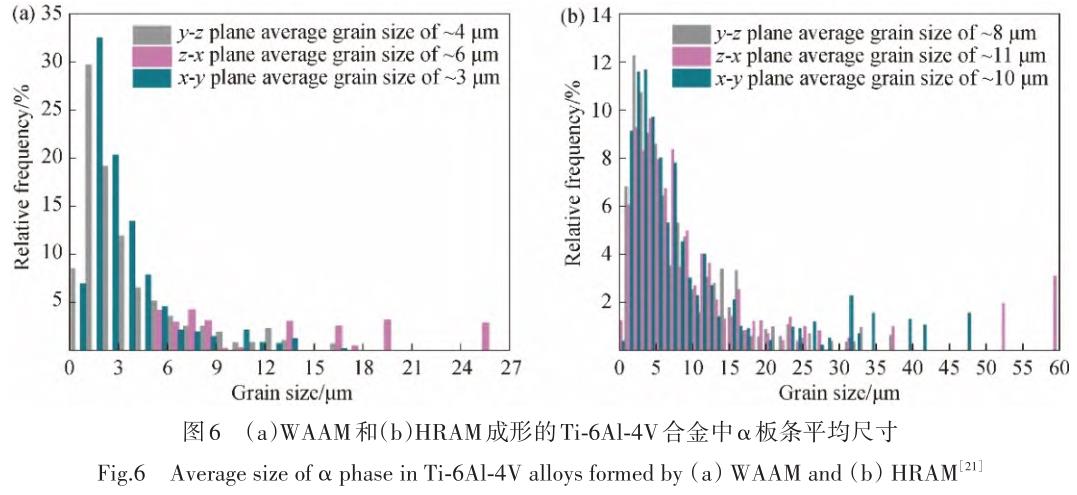
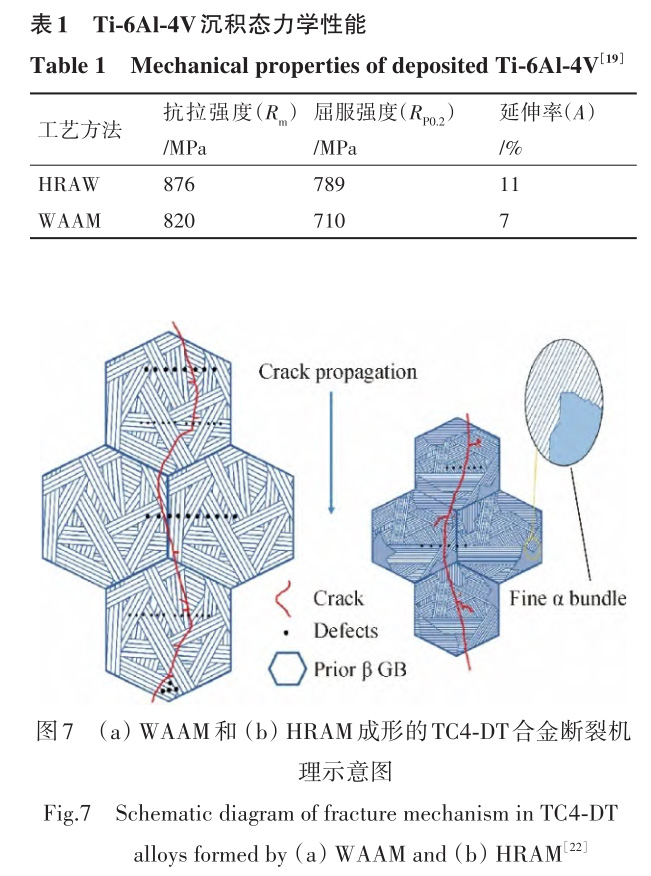
引入微量元素抑制粗大晶粒的形成和生长,成为近年来钛合金WAAM成形的另一个研究热点。添加微量B,在固-液前沿富集造成成分过冷,抑制原始β晶粒的长大。如图9所示,当B含量为0.05%时,在成形的Ti-6Al-4V延伸率保持在8%的前提下,抗拉强度达到1089MPa,提高了17%;但随着B含量的继续增加,Ti与B原位生成脆性TiB第
二相,强度进一步提高,但塑性明显降低[25-26]。另外,研究人员分别尝试添加微量的Y,Si,Sn,Cr,ZrO2,TiN,ZrN等,作为异质形核剂和起到钉扎作用,抑制初生β晶粒的长大,促使柱状晶向等轴晶转变,改善了初生α相尺寸,提高了力学性能[27-31]。
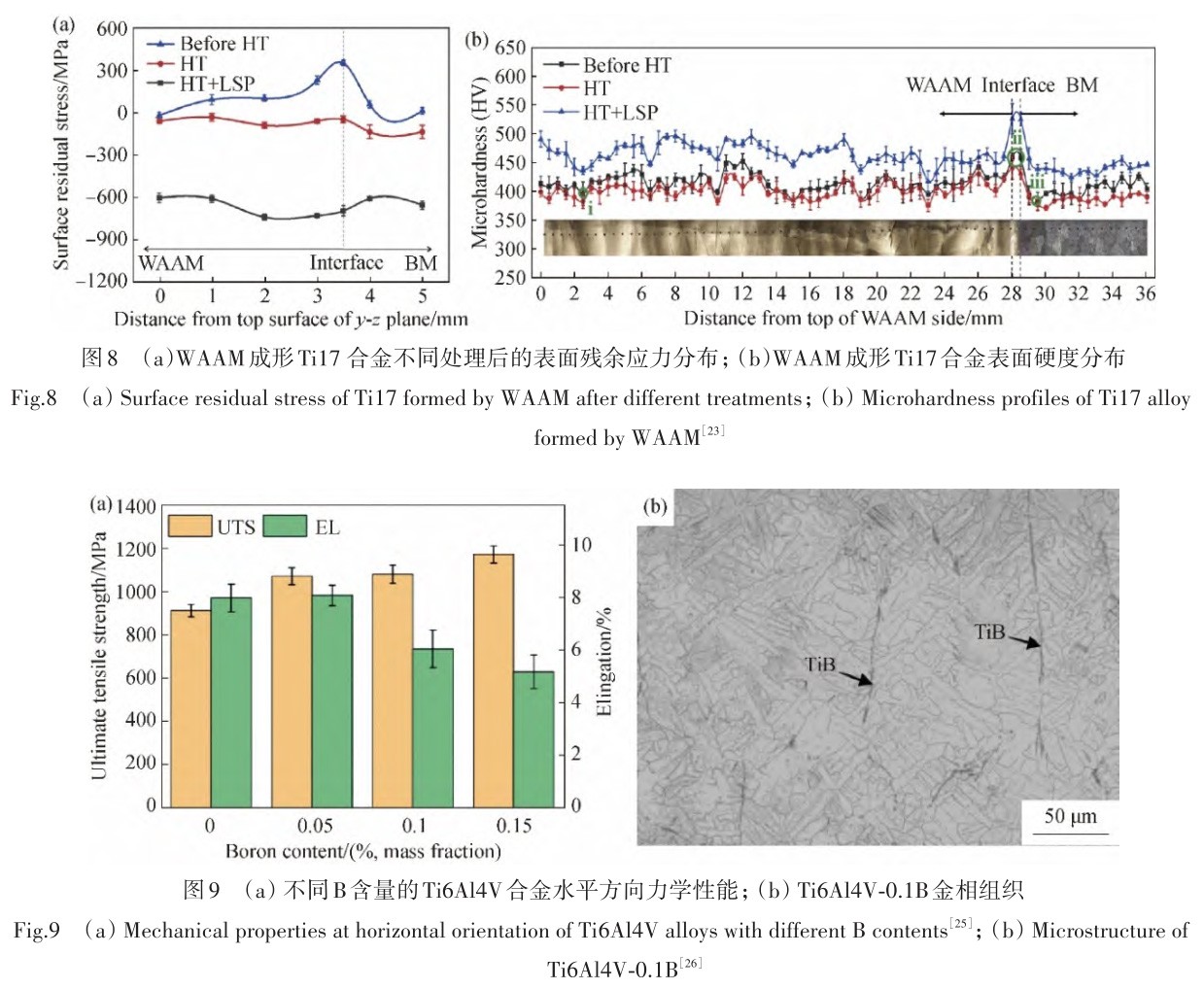
1.2复合制造技术
一方面,对WAAM成形钛合金沉积层进行锤击、辊压轧制、激光冲击,使其产生塑性变形,引入压应力,同时破碎晶粒,从而改善微观组织和性能;另一方面,激光和电弧复合工艺利用激光束热输入稳定,可精确控制熔池尺寸,再结合等离子弧热输入大,可快速熔化丝材的综合优势,提高了沉积效率,实现了大尺寸、表面平整的钛合金构件成形[32-33]。基于传统锻造技术和WAAM相结合,Bambach等[34]提出两种工艺路线用于航空航天零件的制造,第一种采用WAAM制备预成形半成品,然后进行锻造获得最终零件,图10(a)是采用该工艺生产的喷气发动机TC4叶片,其组织与性能超过了铸造与锻造的构件;第二种,采用常规锻造制备预成形件,再通过WAAM成形构件的最终特征,如图10(b,c)所示。两种工艺获得的零件,其力学性能与锻造工艺相当,但工艺灵活性高于传统的单一锻造工艺。
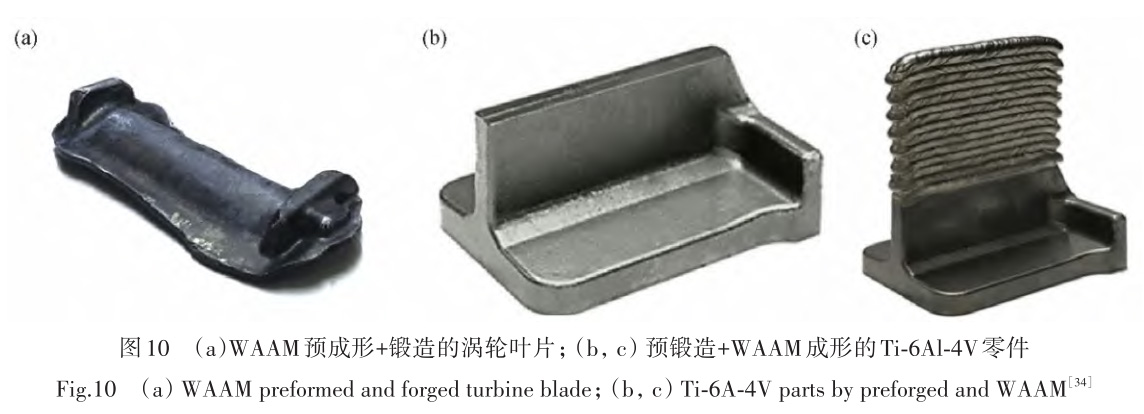
1.3原材料丝材
作为钛合金电弧熔丝增材制造的原材料,丝材表面质量和化学成分对钛合金构件的性能起着重要的作用。目前,电弧增材制造钛合金的研究和应用主要以钛合金焊丝为原材料,相关标准主要有GB/T3623,AMS4954J和ASTMB863,其原材料化学成分按照焊缝性能要求设计,未考虑增材制造过程的化学元素烧损情况。其次,表面质量要求和尺寸精度规定也不符合增材制造实际需求。
研究人员通过对WAAM工艺特点的研究,逐步开展了针对WAAM成形用钛合金丝材的开发。陈荣等[35]设计了一种含有0.06%~0.2%B元素的钛合金丝材,有效抑制了初生β晶粒宽度。商国强等[36]采用冷/热拉拔的方式,制备电弧增材制造用钛合金丝材,其直径公差控制在±0.02mm,椭圆度≤0.02mm,避免了夹丝、断丝、丝材扭滚、送丝不畅等问题,提高生产效率的同时保证了成形尺寸精度,减少了内部缺陷。张斌斌等[37]通过并排捆扎或缠绕的方式将钛合金预制丝材和Ti-6Al-4V丝材的残料相互混合,制备电弧增材用钛合金丝材,实现了构件的低成本制造,经测试,构件抗拉强度Rm≥800MPa,延伸率≥10%,断裂韧性KIC≥100MPa.m1/2。
针对不同强度、不同使用工况的WAAM成形钛合金构件,其专用丝材相继被研制开发和成功使用。
1.4工程化应用
随着钛合金WAAM成形工艺、性能和材料的大量研究以及装备的开发,部分成果逐渐实现了工程化应用。挪威金属3D打印公司NorskTitani⁃umNTi率先采用快速等离子沉积技术(RPD)进行钛合金构件的生产,如图11(a,b)所示,该工艺是经美国联邦航空管理局(FederalAviationAdminis⁃tration,FAA)认证的贴牌生产(originalequipmentmanufacture,OEM)合格的增材制造工艺,可降低零件制造成本30%,缩短交货期6个月,已与法国空中客车公司(Airbus)、美国波音公司(Boeing)、
法国赛峰集团(Safran)等建立合作[38],并与国际合作组织美国汽车工程师学会(SocietyofAutomotiveEngineers,SAE)共同推出了AMS7004《在消除应力Ti-6Al-4V基体上等离子弧直接能量沉积增材制造钛合金预制件规范》和AMS7005《送丝式直接能量沉积增材制造技术工艺规范》[39]。国内西安优弧智熔增材制造有限公司针对等离子弧固定侧向送丝的技术难题,自主研发了侧向送丝万向旋转机构和四轴以上的运行软件,以及配套的高度跟踪系统,实现无人机发动机上梁架、球形气瓶等复杂钛合金构件的快速成型,如图11(c,d)所示,构件性能与锻造工艺相当。北京煜鼎增材制造研究院有限公司发明了多个等离子弧增材制造潜艇全钛耐压壳体,该壳体由内外双层壁和内部加强筋组成,中间可添加吸波材料和降噪材料,提高潜艇的隐身性能[40]。鉴于WAAM成形钛合金组织和性能特点,目前仅部分得到工程化应用,可替代部分铸件,但与锻件水平尚有一定的差距。
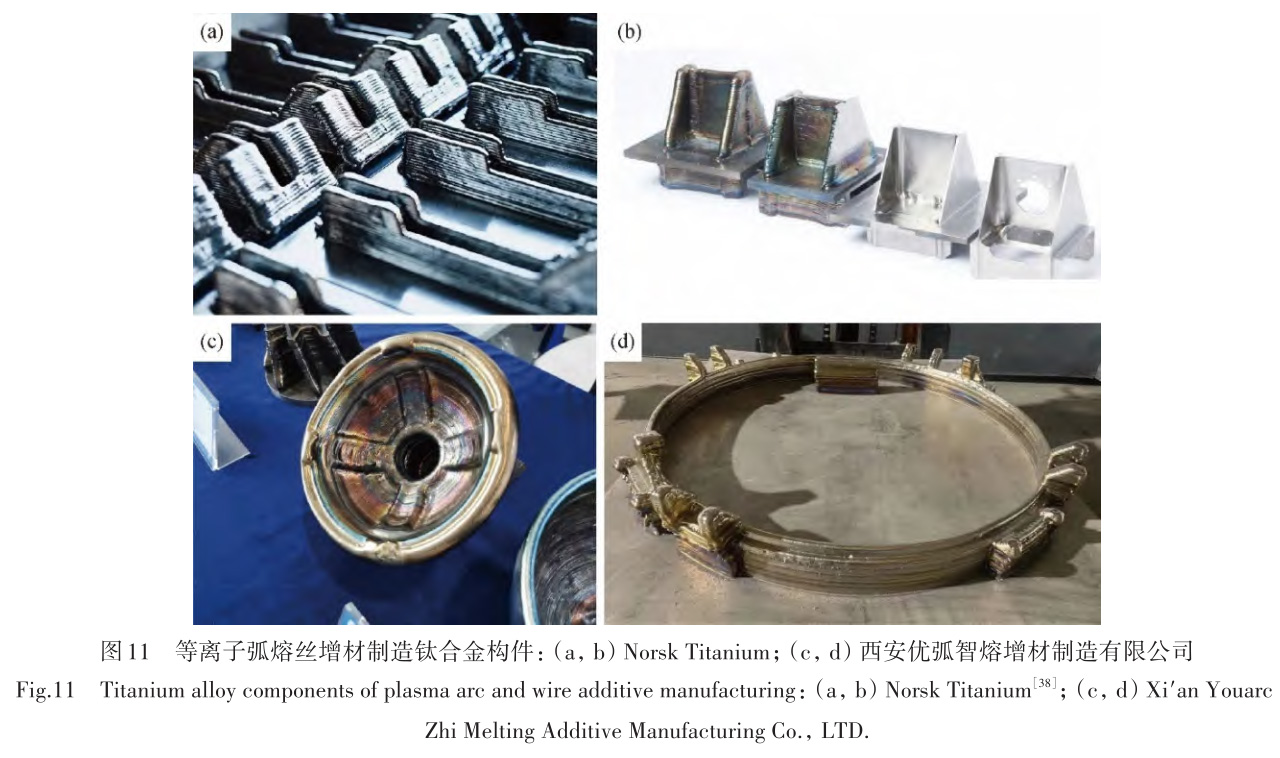
2、电子束熔丝沉积成形技术
2.1组织与性能优化
电子束熔丝沉积快速成形技术具有高的沉积效率、良好的冶金过程、真空环境不会混入O,N,H杂质,适用于钛合金构件的成形制造。王逸尘[41]基于TA15的电子束熔丝沉积成形,研究了束流密度、送丝速度和打印速度对成形构件组织和性能的影响。
黄志涛等[42]针对性采用分块成形、分区成形等方法,使钛合金的电子束熔丝成形变形情况得到改善,实现了沉积过程中尺寸的精确控制。
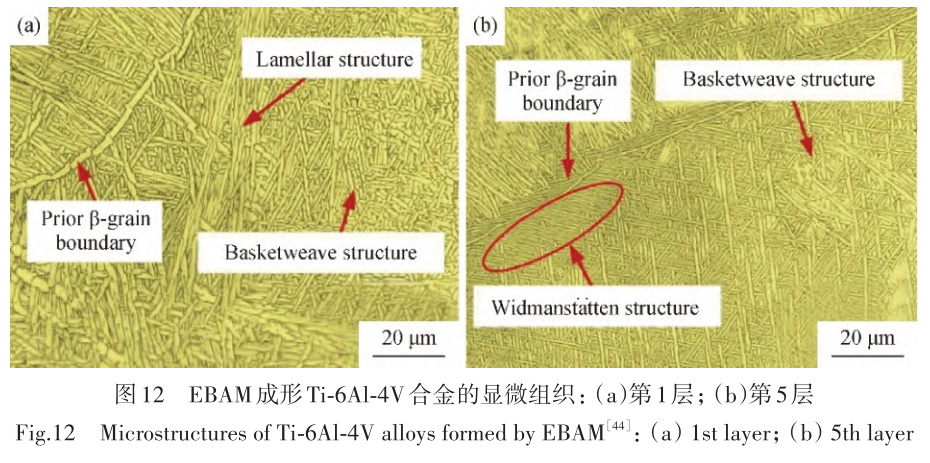
受复杂热循环的影响,钛合金电子束熔丝增材制造成形组织以梯度变化的柱状晶和等轴晶为主,如图12所示,微观组织主要由片层组织、网篮组织和魏氏组织组成[43-44]。通过有限元方法,结合熔池凝固原理,精确控制熔池尺寸,间接提高过冷度和控制凝固速率,可获得等轴组织。新型的同轴电子束熔丝增材制造技术(coaxialelectronbeamwirefeedingadditivemanufacturing,CAEBWAM)如图13(a)所示,将丝材通过锥形的电子束中心进行熔化,相比侧向送丝,熔池更稳定,过冷度更低,凝固速率更高。图13(b)显示:成形的Ti-6Al-4V合金组织宏观上由细化的等轴晶组成,微观下晶界α相呈不连续状,晶内片层α相较短,经过表2不同的热处理后[即炉冷(FC)和空冷
(AC)],可获得较高的强度和塑性,各项异形明显减弱[45-48]。其次,研究发现选用纯Cu和纯Ti组合基材,同样能够增加温度梯度,提高凝固速率,获得强度和塑性匹配较好、各向异性较小的钛合金构件[49]。
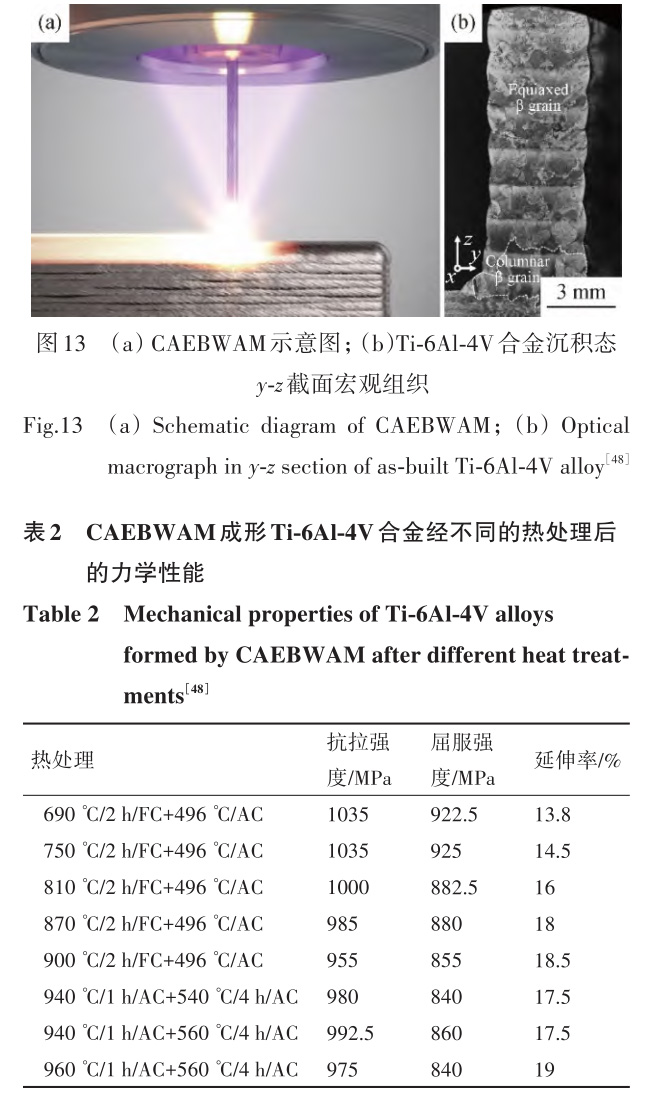
由于EBAM工艺需要在真空条件下进行,这对处于高温的沉积金属进行形变处理而言非常困难,研究人员主要通过添加微量元素尝试改善组织性能。C和B元素被证明可以促使柱状β晶粒转变为等轴晶,并可以提高强度和塑性。然而,随着Ti与C,B生成脆性相,塑性出现了明显的降低[50]。难熔金属元素Mo,W,Nb等在高温液态熔池中稳定,可细化粗大的β晶粒,但部分未熔化的颗粒对构件力学性能存在不利影响。Ti-Cu合金具有高的成分过冷能力,在高的冷却速率和温度梯度下,可形成完全等轴晶粒和超细共析组织
[51]。如图14所示,采用化学镀在Ti-6Al-4V丝材表面制备厚度约为10µm的Cu镀层,以原位合成的方式进行EBF3成形,Cu有效抑制了初生β晶粒的长大,出现非均质形核,成形组织为柱状晶和等轴晶的混合结构,β相边界析出的Ti2Cu具有沉淀强化作用,水平方向(horizontaldirection,即H)和竖直方向(verticaldirection,即V)抗拉强度提高约170MPa,均实现了强度和韧性的良好匹配[52-53]。
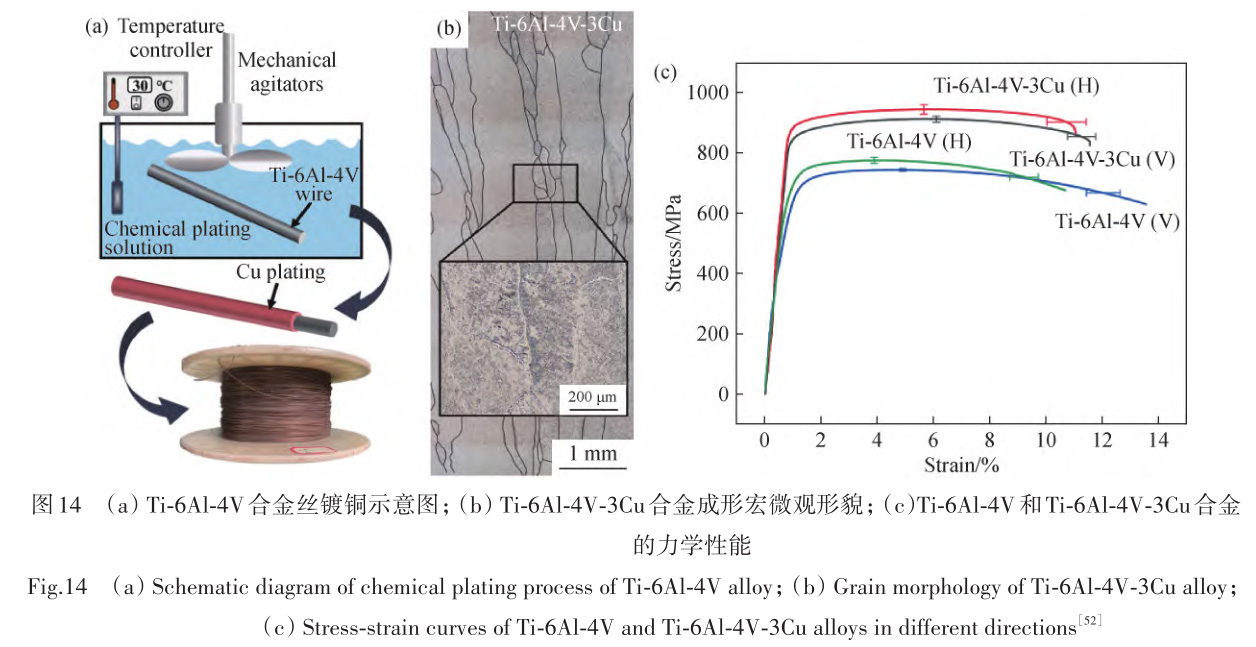
2.2复合制造技术
通过电子束熔丝增材制造与传统锻造的结合应用,实现大型钛合金构件的制造或修复,成为工业化应用的一个重要方向。靳文颖[54]针对发动机扭曲叶片的端部损伤问题,采用TC4钛合金薄壁平板模拟叶片端部,利用电子束熔丝增材制造工艺进行修复试验,通过计算机模拟仿真分析温度场,认为层间间隔时间是决定沉积层温度分布均匀性的重要因素,制定了单向/往复和单/双道成形工艺,并采用自制TC4EH丝材作为成形原材料,图15显示的成形构件整体由基材热影响区、“层带”结构区、无“层带”表现的均匀区和表层等轴区组成,抗拉强度和延伸率分别达到基材的94%和90%。王宁宁等[55]在开展TC11钛合金电子束熔丝增材制造工艺研究的基础上,探索“增材+锻造”复合制造大型钛合金构件,利用正交试验法对束流、运动速度、送丝速度和扫描模式等参数进行优化,并参考GJB2744A《航空用钛及钛合金锻件规范》,通过图16的测试结果发现,沉积部分以及与锻件结合处的拉伸性能均高于规范要求,而延伸率和断面收缩率却低于规范要求。
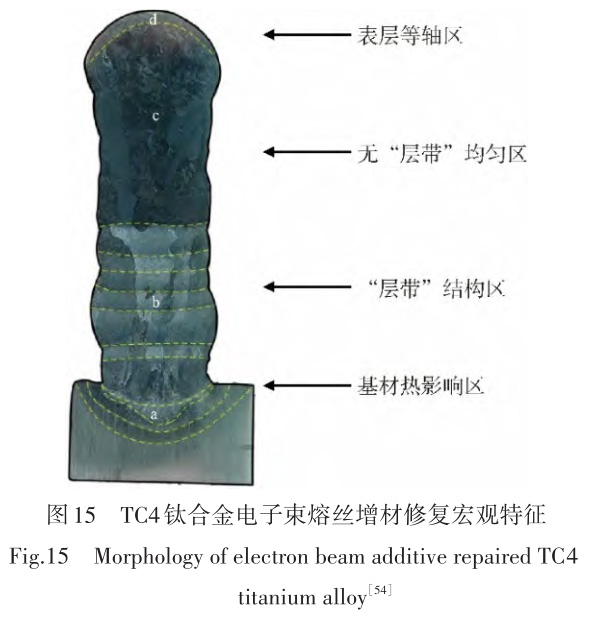
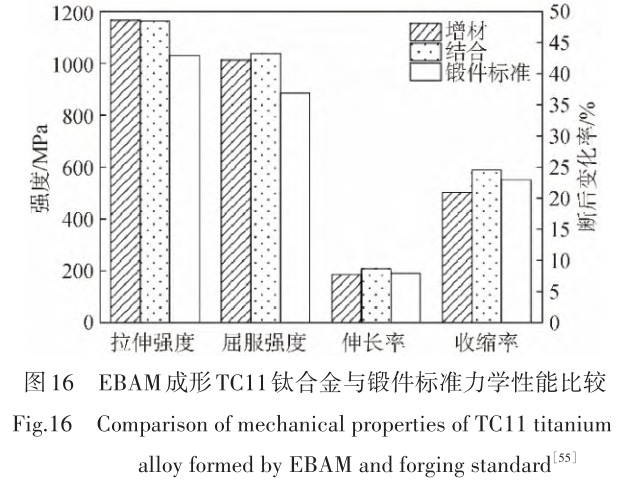
2.3原材料丝材
近年来,研究人员针对电子束熔丝沉积快速成型工艺特点,逐步开展了不同强度级别的专用钛合金丝材的研制,相关结果见表3。北京航空制造工程研究所利用Al,V,O等元素对钛合金的强韧化机制,结合电子束熔丝沉积快速成型工艺特点,在严格控制Al,V元素含量的基础上,增加O元素含量,成形构件抗拉强度可达到860MPa以上,冲击韧性和断裂韧性分别达到65J/cm2和106MPa.m1/2以上,实现了强度和塑韧性的良好匹配[56]。随后,又相继开发出抗拉强度为920MPa和960MPa级α+β型钛合金丝材,
塑性延伸率在5.7%~9.3%之间[57-58]。中国船舶重工集团公司第七二五研究所利用Al,Zr,Nb,Mo合金元素的固溶强化作用及其对增材制造塑韧性的影响机制,开发出强度为780MPa级的电子束熔丝沉积用钛合金丝材,成形构件抗拉强度超过780MPa,延伸率和冲击韧性分别达到10%和50J以上,综合性能可满足海洋工程领域用电子束熔丝沉积钛合金构件的需求[59]。北京航空材料研究院通过优化调整TA15钛合金丝材中Mo,V,O的含量,经热处理后,其抗拉强度达到960MPa以上,延伸率超过了15%,并且各向异性弱化至5%以下[60]。
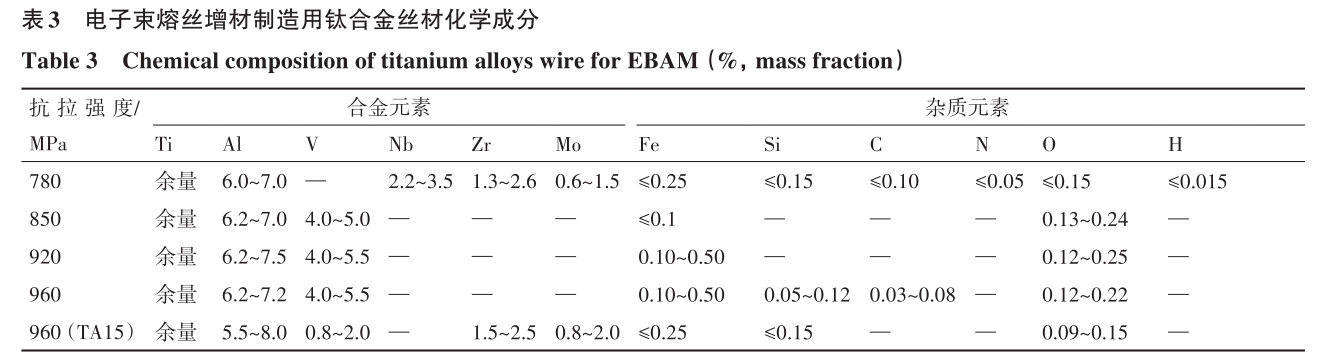
2.4工程化应用
钛合金电子束熔丝沉积快速成形技术具有高的沉积效率、良好的冶金过程、真空环境杂质含量少、表面氧化膜更稳定、耐电偶腐蚀性能更优异等特点,得到了美国波音公司(Boeing)、法国空中客车公司(Airbus)、美国洛克希德.马丁空间系统公司(LockheedNartinSpaceSystemsCompany)等国际航空航天企业的重点关注。2009年,美国3D打印技术制造商Sciaky推出了电子束熔丝增材制造装备,并于2011年与洛克希德.马丁公司开展合作,实现了F-35战斗机钛合金零件的快速制造,截至2022年可实现每小时18kg的沉积速率[61],图17(a)为该公司制造的钛合金毛坯件。中国航空制造技术研究院于2006年开始电子束熔丝沉积快速成形技术的研究,目前已开展了TC4,TA15,TC18等多种牌号钛合金的工艺试验,同时也开发了多规格钛合金构件的制造,并获得装机测试验证,图17(b)为电子束增材制造和机加工处理后的钛合金零件。
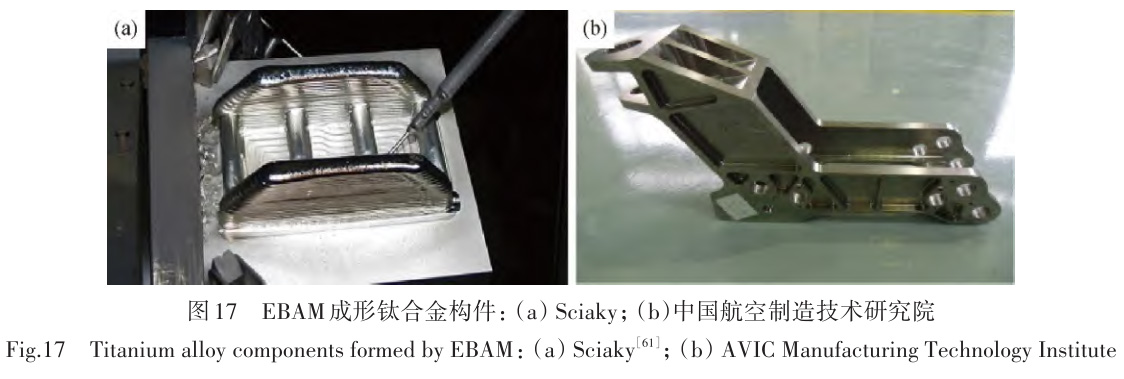
3、激光熔丝增材制造技术
3.1组织与性能优化
基于粉末的激光增材制造钛合金构件,其综合力学性能可与锻件性能相媲美,已获得大量的应用。但粉末材料制造成本相对较高,而且成形零件内部易产生气孔,对韧性和疲劳性能有一定的影响[62-63]。钛合金丝材对激光的吸收率较低,一定程度上限制了钛合金激光熔丝增材制造技术的应用。Mok等[64-65]使用半导体激光熔化Ti-6Al-4V
钛合金丝材,分析了送丝方向、送丝角度、送丝速度、进给速度和激光能量等对沉积形貌的影响规律,明确了以45°方向和2m/min送丝速度进行前送丝,可获得致密、无气孔、表面光滑平整的成形构件。其中,激光能量对沉积宽度起决定性的作用,而送丝速度主要影响沉积高度。激光熔丝成形钛合金宏观组织表现为外延生长的粗大β晶粒
和层带结构,微观呈现网篮组织和魏氏组织的混合结构,如图18所示。
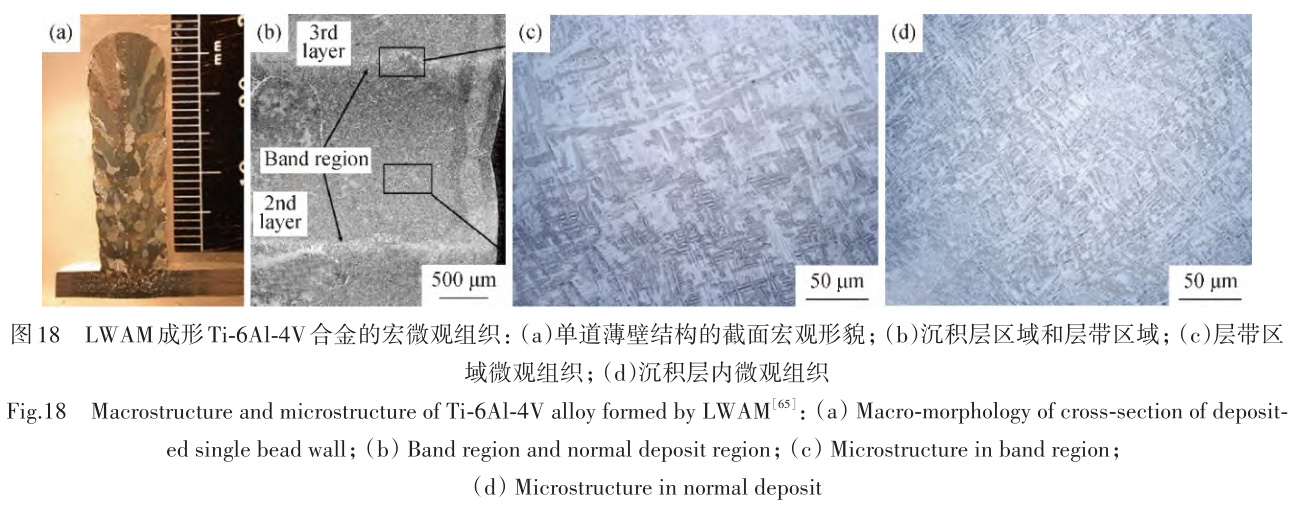
图19为LWAM成形TC4-DT合金经固溶-时效处理后的显微组织。可以看出,经过热处理后,TC4-DT合金微观组织结构由粗大柱状晶转变为等轴晶+柱状晶的双相结构,晶界α集束依然存在[66-67]。Yuan等[68]将超声能场以同步耦合的方式引入激光熔丝增材制造中,有效抑制了初生β晶粒的外延生长趋势,弱化了织构,促使等轴晶形成,如图20所示。同时,对沉积金属进行超声波冲击时效处理,实现在线调控内部残余应力,降低了构件变形开裂倾向。严家印[69]探索了循环热处理、脉冲电流处理和超声微锻造+固溶时效处理等方法对LWAM成形TC4钛合金的影响,结果如图21所示。可以看出,激光熔丝成形循环热处理、脉冲电流处理和超声微锻造+固溶时效处理均改善了TC4钛合金激光熔丝沉积成形构件的组织和性能。循环加热处理通过淬火预处理切断魏氏组织的遗传性,再通过控制加热速率和冷却速率,进行如图22所示的多次循环热处理,使针片状α向片层状α转变,马氏体α'和晶界α集束逐渐消失,显微组织由魏氏组织向网篮组织转变。脉冲电流处理则根据不同的平衡温度对应不同的脉冲电流,选用频率为200Hz的脉冲电流处理沉积态试样,使马氏体α'逐渐发生分解,针片状α粗化成团状和厚片状,并出现一定程度的聚集。超声微锻造是将TC4沉积态试样以振幅为80%、功率为1800W、压力为80N的参数进行处理,沉积金属产生一定程度的变形、再结晶,致使凝固的枝晶破碎,晶粒细化,然后进行950℃/WC(WC:水冷)/1h+550℃/AC/4h的固溶-时效处理,致使高纵横比的针状α向低纵横比的针状和团状α转变,针状马氏体α'发生分解。3种处理工艺均降低了成形件的显微硬度、屈服强度和抗拉强度,而延伸率大幅度提升,开拓了新型后处理方法。
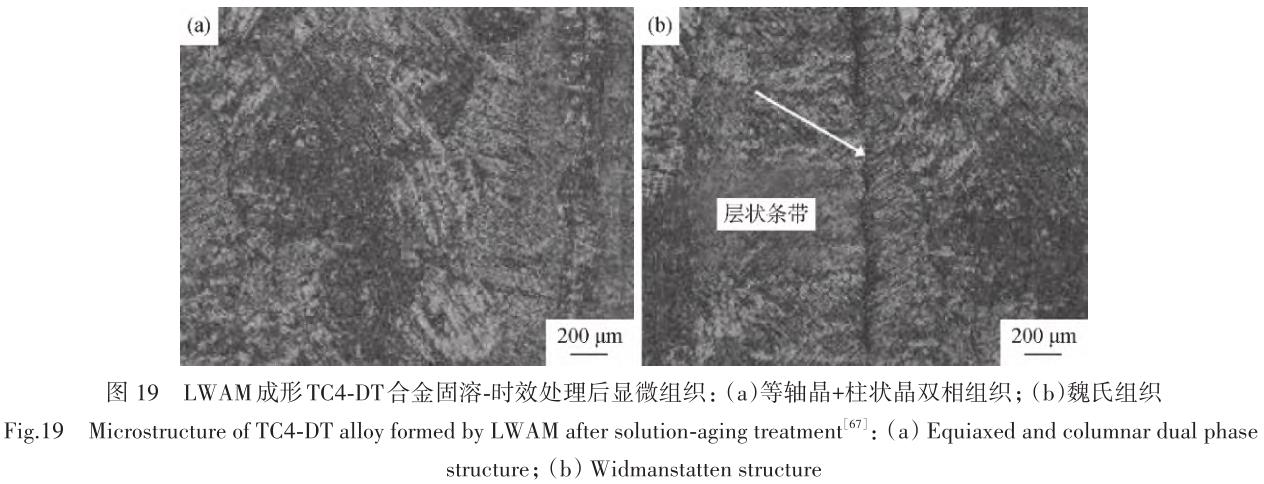
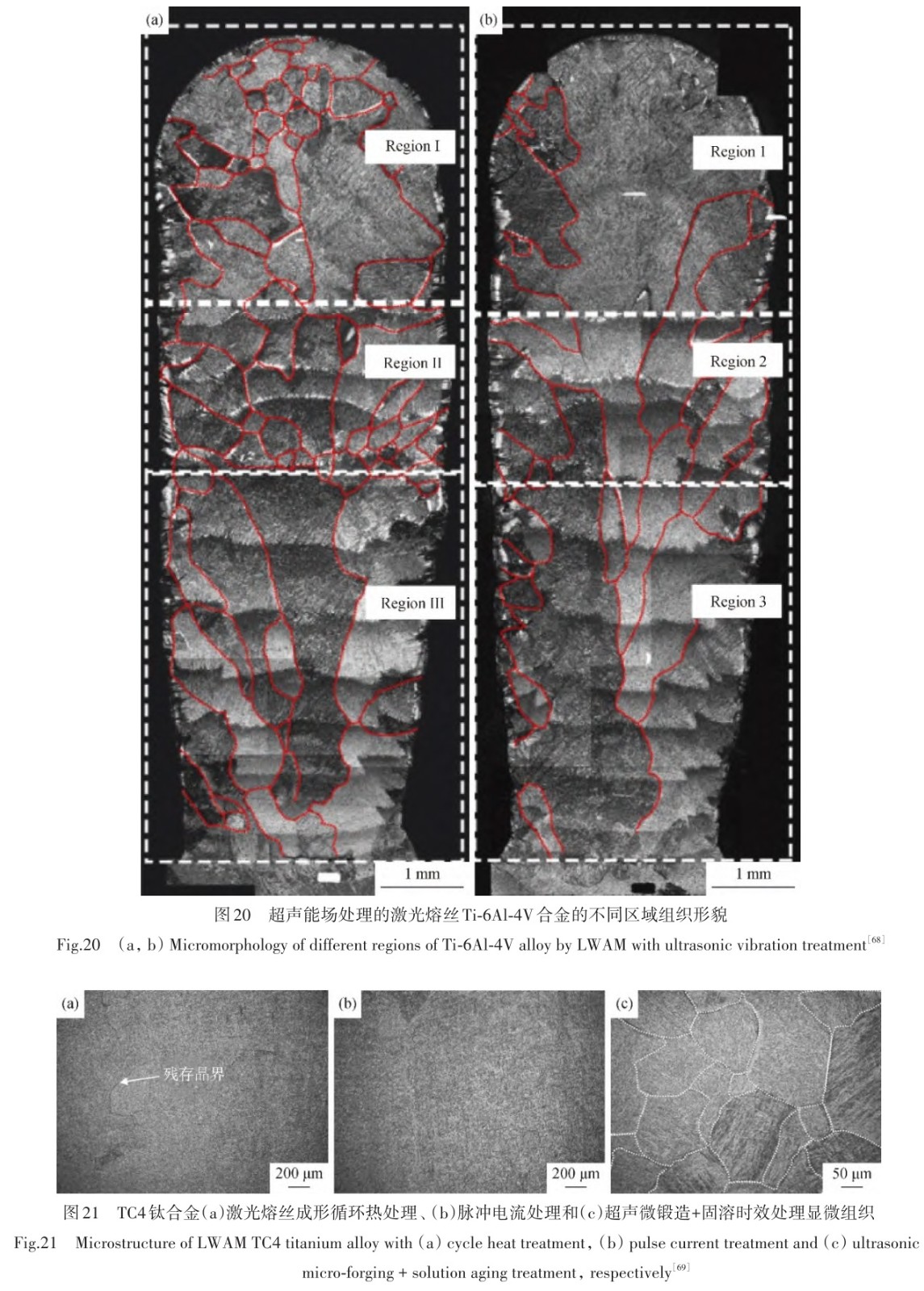
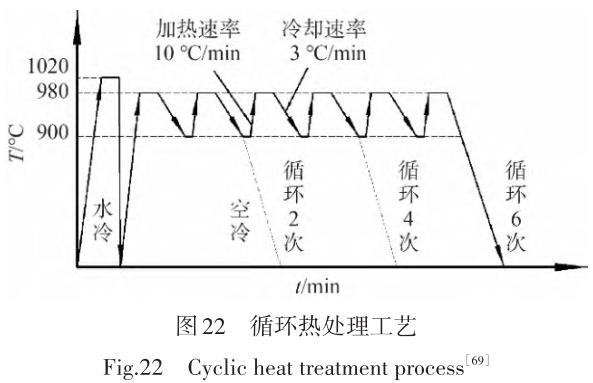
针对激光熔丝的光丝不同轴,加工自由度受限,成形表面粗糙度大的固有工艺缺陷,Ding等[70]采用图23(a)所示的轴对称多激光源垂直送丝进行Ti6Al4V合金成形试验,可避免上述缺陷,同时弱化了成形金属的各向异性,但激光聚焦关键模块设备复杂、成本高。图23(b,c)显示的同轴送丝的单束激光熔丝增材设备相对较为简单,成形TC4钛合金横向和纵向的粗糙度分别为1.7~9.3µm和29.6~36.3µm,显微硬度为HV340~400,呈现先增大后减小的趋势,而侧向送丝的显微硬度为HV310~500,随着沉积高度的增加而增加[69,71-72]。如图24所示,同轴送丝的激光熔丝增材制造钛合金构件抗拉强度、屈服强度和延伸率分别为1007~1060MPa,949~999MPa和7.5%~9.7%,综合性能明显优于侧向送丝和循环热处理、脉冲电流处理结果[73]。
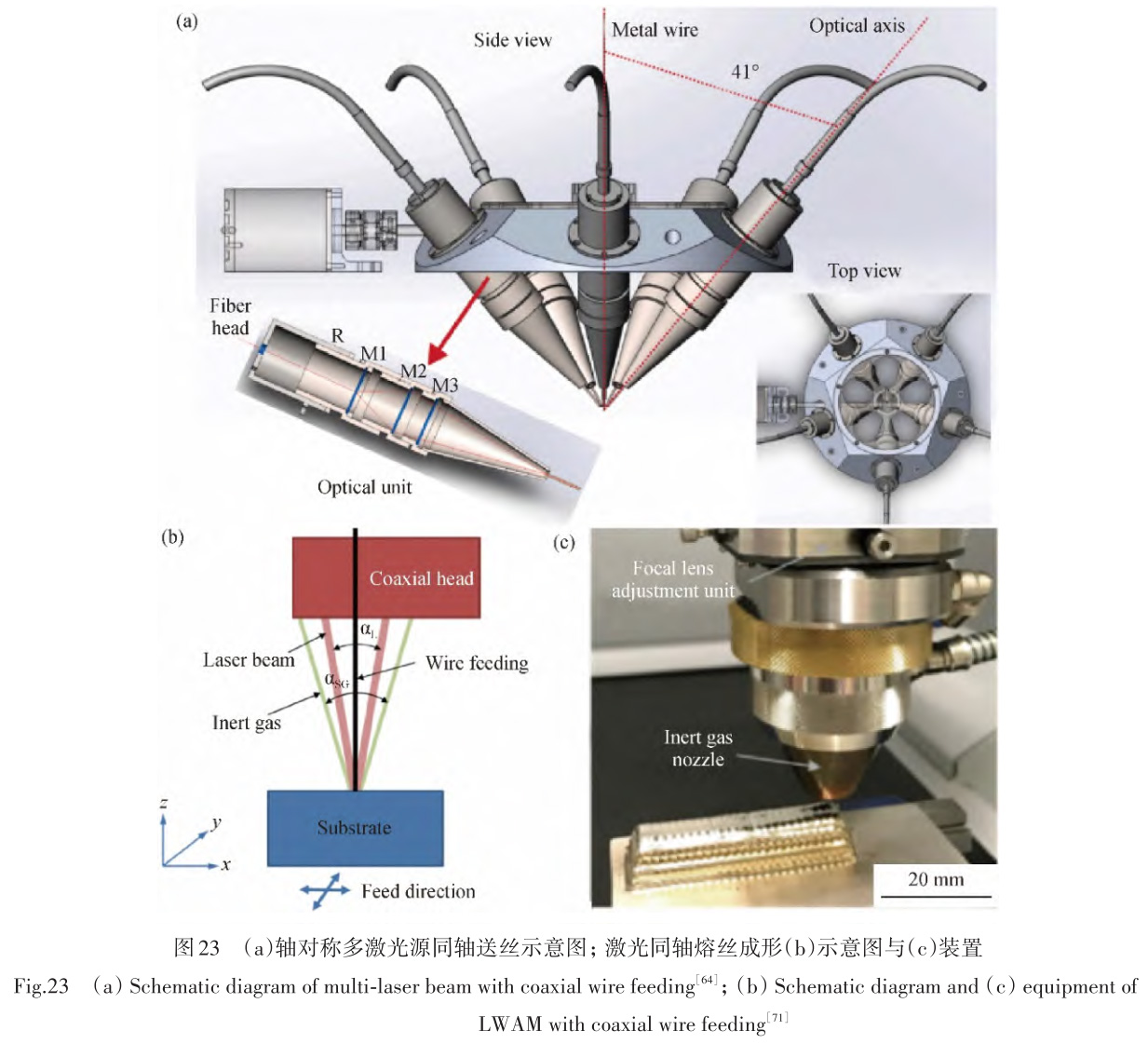
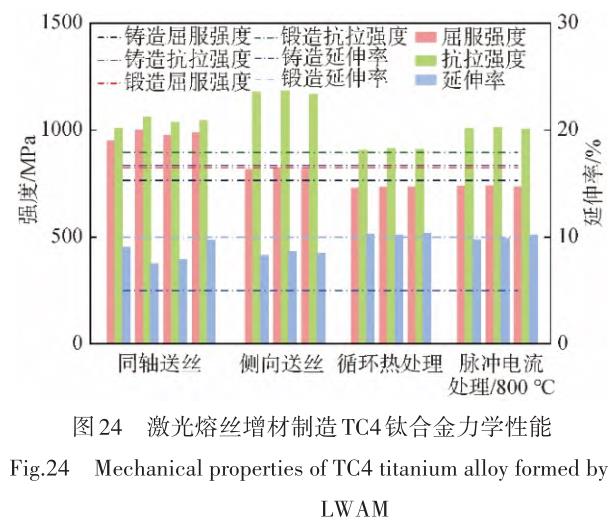
3.2复合制造技术
激光功率输出恒定,通过单独控制激光功率和能量分布,可获得稳定的熔池,避免形成匙孔效应,叠加电弧的高能量转换效率,复合热源下的沉积速率明显高于单一的电弧热源或激光热源。由图25可知,当热输入恒定为8kW时,激光-电弧复合热源的沉积效率达到3kg/h,明显高于单一电弧或激光热源的沉积效率。Wang等[32]通过优化等离光热源的分布距离,实现TC4钛合金在高沉积效率下的近净成形,其沉积宽度在一定范围内可控。
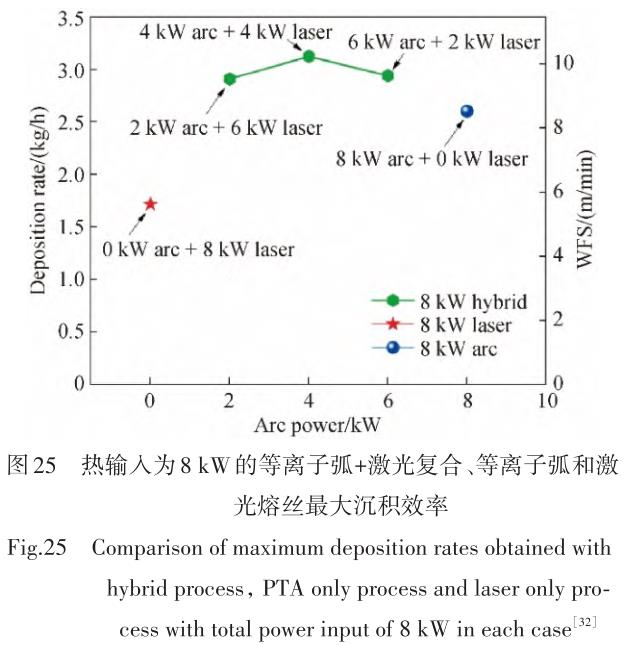
为了克服能量集中导致沉积金属重熔,进一步引入两个激光热源分布在PTA热源两侧后方,改善了重熔金属比例。
3.3原材料丝材
钛合金激光熔丝增材制造用丝材与电弧、电子束熔丝基本相同,鉴于丝材对激光功率的反射作用,哈尔滨焊接研究所有限公司发明了如图27所示的一种麻花绳状的TC4丝材用于激光熔丝增材制造,该丝材采用3根直径为0.65~0.74mm的细丝旋转组合成直径为1.2~1.6mm的丝材,使激光束与丝材在工件表面相交时与单丝重叠,同时丝材中添加了2.0%~2.5%的低熔点元素Sn,并将α稳定元素Al的含量提高到6.9%~7.4%,从而降低了丝材的熔点,实现了低热输入和高的沉积效率[74]。钛合金的激光熔丝相对于电弧、电子束起步较晚,其专用丝材的开发鲜有报道,仍需要对工艺特点进行深入研究,从而开发适用于该工艺的专用丝材。
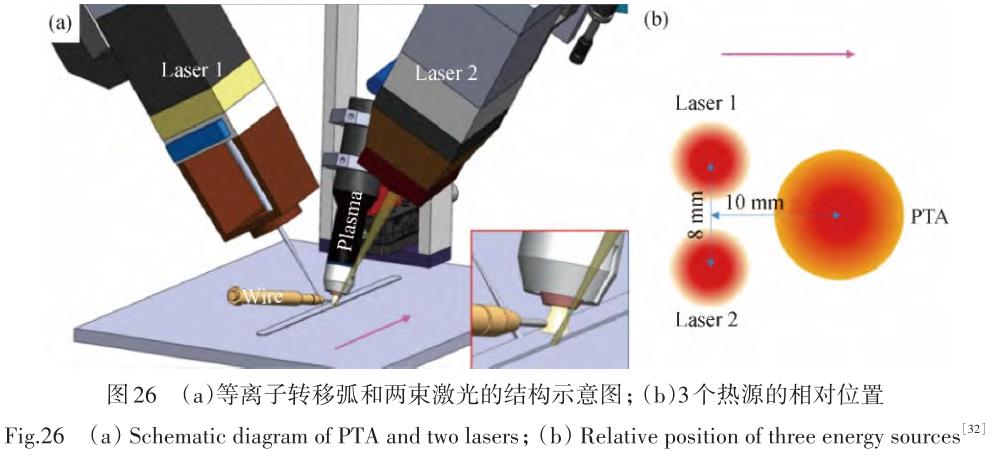
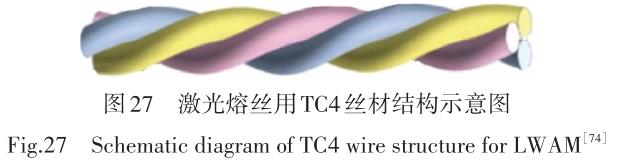
3.4工程化应用
相对于电弧和电子束,关于激光熔丝增材制造钛合金的应用报道较少。西安交通大学方学伟等[75]基于同轴送丝的激光熔丝增材制造技术,开发出了针对大型钛合金零件成形装置及方法,克服了大型防氧化装置需定制、周期长、成本高的难题,可实现任意尺寸的钛合金零件自由制造,同时,对沉积表面的氧化层进行实时激光清洗,可保证层间良好的结合,但尚未见到相关零件制造的报道。北京卫星制造厂有限公司祁俊峰等[76]利用激光熔丝增材制造技术,调整脉冲宽度、摆动频率和幅度,解决了钛/铝异质合金构件成形尺度、致密度及界面等问题,实现高性能钛/铝异质合金复杂结构的制造。吉凯恩航空航天公司研发成功并投入使用了世界上最大的激光熔丝沉积增材制造生产单元Cell3,该单元配备激光器功率达到20kW,运动轴多达10个,配备大面积惰性保护气氛,最大基材尺寸为5.6m×2.5m,可成形长度最大为5m的钛合金构件。
4、总结与展望
基于钛合金丝材的增材制造技术,由于温度梯度的影响,成形组织宏观上呈外延生长的粗大柱状晶和层带结构,微观上主要由具有网篮特征的魏氏组织和针状马氏体α'构成,导致成形构件组织不均匀,力学性能不均匀,以及严重的各向异性。通过优化成形工艺、添加微量元素、后热处理工艺以及层间复合处理等方法,虽然在一定程度上细化了晶粒,获得柱状晶+等轴晶的混合组织,强度和塑性得到改善,但各向异性依然明显,与传统锻造工艺获得的组织性能仍存在一定的差距。
然而,在控形方面,通过升级装备和优化工艺,加之实时监控系统,致使成形构件内部致密、无缺陷,构件尺寸精度进一步提高,可成形较为复杂的构件,并且后期加工余量减少,可与同轴送粉技术相媲美。
国内外大型钛合金结构件,无一例外地均采用重型真空自耗炉熔炼钛铸锭,通过多火次自由锻造+机加工工艺完成,制造周期长,材料浪费大。
如钛合金空-空导弹弹头和弹体的材料利用率仅为15%。而基于钛合金丝材的金属增材制造技术,无需真空熔炼系统,材料利用率达到90%以上,成形金属成分均匀、无偏析,成形构件尺寸不受限制,但存在机械性能不均匀,无法达到高端结构件的性能要求,主要原因在于缺少在热-力耦合作用下,迫使金属产生塑性流动,发生动态再结晶的过程。因此,将金属熔丝增材制造与传统锻造工艺结合,可兼具增材制造成分无偏析、柔性成形、材料利用率高,以及锻造产生塑性变形促进动态再结晶的诸多优点。通过增材制造实现预制件的成形,获得锻造毛坯,相对传统的自由锻,工序明显减少,制造周期缩短和成本大幅度降低。
用于钛合金丝材增材制造的原材料主要为传统的焊丝,焊接过程中焊缝金属作为母材连接部分,受母材约束强化作用,强度可达到母材的90%以上,而增材制造实质上是“焊缝金属”逐层堆积成构件,应认识到其性能和母材在本质上有一定的区别。因此,应充分考虑避开传统的焊接用丝材原材料,根据电弧、电子束和激光熔丝增材制造工艺特点,以及化学成分、表面质量、尺寸精度、温度场等对增材制造成形过程稳定性、成形组织等的重要影响,结合各应用领域要求,针对性地开发专用丝材。其次,目前基于钛合金丝材的增材制造,其性能评价主要参考相关的锻件和铸件规范。随着钛合金丝材增材制造技术的广泛研究和应用,应逐步推进相关标准的起草和审定,促进该技术的持续突破和完善以及更大范围的应用。
随着各种技术的不断迭代升级,基于钛合金丝材的增材制造技术经历了前期的探索、开发阶段,近两年来逐渐在航空航天、国防军工、核电能源等领域开始小批量生产应用,标志着该技术迈入了初级生产阶段,技术和装备也迎来急速发展时期。相信随着技术的持续突破和标准体系的日趋完善,市场也将趋于成熟,低成本化的钛合金丝材增材制造技术将走进各行各业。
参考文献:
[1]雷 霆 . 钛 及 钛 合 金[M]. 北 京 : 冶 金 工 业 出 版 社 ,2020: 3.
[2]ZHAO Q Y, SUN Q Y, XIN S W, et al. High-strength titanium alloys for aerospace engineering applications: a review on melting-forging process [J]. Materials Science & Engineering A. 2022: 845: 1.
[3]任庆华, 张利军, 薛祥义, 等 . 钛合金在轻量化地面武器装备中的应用[J]. 世界有色金属, 2017(20):1-4.
[4]徐全斌, 刘诗园 . 国外航空航天领域钛及钛合金牌号及应用[J]. 世界有色金属, 2022(16): 96-99.
[5]LIU S H, LI C X, ZHANG H Y, et al. A novel structure of YSZ coating by atmospheric laminar plasma spraying technology [J]. Scripta Materialia, 2018(153): 73-76.
[6]MONTGOMERY J S, WELLS M G H. Titanium armor applications in combat vehicle [J]. JOM, 2001, 53(4): 29-32.
[7]郑超, 朱秀荣, 王军, 等 . 装甲钛合金的研究与应用现状[J]. 钛工业进展, 2020, 37(4): 41-48.
[8]李涤尘, 鲁中良 田小永, 等 . 增材制造——面向航空航天制造的变革性技术[J]. 航空学报, 2022, 43(4):22-38+3.
[9]卢秉恒 . 增材制造技术——现状与未来[J]. 中国机械工程, 2020, 31(1): 19-23.
[10] 梁朝阳, 张安峰, 梁少端, 等 . 高性能钛合金激光增材制造技术的研究进展[J]. 应用激光, 2017, 37(3):452-458.
[11] 陈玮, 李志强 . 航空钛合金增材制造的机遇和挑战[J]. 航空制造技术, 2018, 61(10): 30-37.
[12] LIN Z D, SONG K J, YU X H. A review on wire and arc additive manufacturing of titanium alloy [J]. Journal of Manufacturing Process, 2021, 70(3): 24-45.
[13] 滕树满 . 电弧熔丝增材制造研究进展(待续)[J]. 有色金属加工, 2022, 51(1): 21-29.
[14] WU B T, PAN Z X, DING D H, et al. A review of the wire arc additive manufacturing of metals: properties,defects and quality improvement [J]. Journal of Manu⁃facturing Processes, 2018, 35(10): 127-139.
[15] WILLIAMS S W, MARTINA F, ADDISON A C, et al.Wire+arc additive manufacturing [J]. Materials Science and Technology, 2016, 32(7): 641.
[16] 林建军 . 脉冲等离子弧增材制造 Ti-6Al-4V 合金组织演变机理及力学性能研究[D]. 上海:上海交通大学,2017.
[17] XU T Q, LIU J W, WANG J C, et al. Layer control method and mechanical anisotropy of titanium alloy based on double-hot-wire arc additive manufacturing [J]. Journal of Manufacturing Processes, 2022, 82:448-460.
[18] XU T Q, ZHANG M, WANG J C, et al. Research on high efficiency deposition method of titanium alloy based on double-hot-wire arc additive manufacturing and heat treatment [J]. Journal of Manufacturing Processes,2022, 79: 60-69.
[19] MCANDREW A R, ROSALES M A, COLEGROVE P A, et al. Interpass rolling of Ti-6Al-4V wire+arc addi⁃tively manufactured features for microstructural refine⁃ment [J]. Additive Manufacturing, 2018, 21:340.
[20] HÖNNIGE J R, COLEGROVE P, WILLIAMS S. Im⁃provement of microstructure and mechanical properties in wire+arc additively manufactured Ti-6Al-4V with ma⁃chine hammer peening [J]. Procedia Engineering,2017, 216: 8-17.
[21] HU Y N, AO N, WU S C, et al. Influence of in situ mi⁃cro-rolling on the improved strength and ductility of hy⁃brid additively manufactured metals [J]. Engineering Fracture Mechanics, 2021, 253: 107868.
[22] GAO Y F, WU C D, PENG K, et al. Towards superior fatigue crack growth resistance of TC4-DT alloy by in-si⁃tu soled wire-arc additive manufacturing [J]. Journal of Materials Research and Technology, 2021, 15: 1395-1407.
[23] CHI J X, CAI Z Y, WAN Z D, et al. Effects of heat treatment combined with laser shock peening on wire and arc additive manufactured Ti17 titanium alloy: mi⁃crostructures, residual stress and mechanical properties [J]. Surface & Coating Technology, 2020, 396:125908.
[24] 何智. 超声冲击电弧增材制造钛合金零件的组织性能研究[D]. 武汉:华中科技大学, 2016.
[25] YANG Z W, FU L Q, WANG S L, et al. Balance of strength and plasticity of additive manufactured Ti-6Al-4V alloy by forming TiB whiskers with cyclic gradient distribution [J]. Additive Manufacturing, 2021, 39:101883.
[26] 张飞奇 . 基于丝材电弧增材制造 Ti6Al4V-xB 合金的组织性能及模拟[D]. 西安:西安理工大学, 2017.
[27] ZHUO Y M, YANG C L, FAN C L, et al. Effects of trance Sn and Cr addition on microstructure and mechan⁃ical properties of TC17 titanium alloy repaired by wire arc additive manufacturing [J]. Journal of Alloys and Compounds, 2021, 888: 161473.
[28] ZHUO Y M, YANG C L, FAN C L, et al. Effect of di⁃ameter and content of zirconium dioxide on the micro⁃structure and mechanical properties of the TC17 titani⁃um alloy repaired by wire arc additive manufacture [J].Journal of Alloy and Compounds, 2022, 893: 162295.
[29] KENNEDY J R, DAVIS A E, CABALLERO A E, et al.β grain refinement by yttrium addition in Ti-6Al-4V wire-arc additive manufacturing [J]. Journal of Alloys and Compounds, 2022, 895: 162735.
[30] MEREDDY S, BERMINGHAM M J, STJOHN D H, et al. Grain refinement of wire arc additively manufactured titanium by the addition of silicon [J]. Journal of Alloys and Compounds, 2017, 695: 2097-2013.
[31] KENNEDY J R, DAVIS A E, CABALLERO A E, et al. The potential for grain refinement of wire-arc additive manufactured (WAAM) Ti-6Al-4V by ZrN and TiN in⁃oculation [J]. Additive Manufacturing, 2021(40):101928.
[32] WANG C, SUDER W, DING J L, et al. Wire based plasma arc and laser hybrid additive manufacture of Ti-6Al-4V [J]. Journal of Materials Processing Techology,2021, 293: 117080.
[33] WANG C, SUDER W, DING J L, et al. Bead shape control in wire based plasma arc and laser hybrid addi⁃tive manufacture of Ti-6Al-4V [J]. Journal of Manufac⁃turing Processes, 2021, 68: 1849-1859.
[34] BAMBACH M, SIZOVA I, SYDOW B, et al. Hybrid manufacturing of components from Ti-6Al-4V by metal forming and wire-arc additive manufacturing [J]. Jour⁃nal of Materials Processing Tech, 2020, 282(4):116689.
[35] 陈荣, 谭成文, 聂志华, 等 . 一种电弧增材制造用钛合金丝材及其应用:CN108857148A[P]. 2018-11-23.
[36] 商国强, 朱知寿, 王新南, 等 . 一种等离子弧/电弧增材制造用钛合金丝材加工方法: CN112517659B[P].2023-01-13.
[37] 张斌斌, 钟永腾, 周余庆, 等 . 一种电弧增材用低成本钛合金丝材及其结构件的制造方法: CN114351004A[P]. 2022-04-15.
[38] 夏沐清 . 美国 Norsk Titanium 公司交付波音 787 梦想(dreamliner)客机 3D打印钛零件[J]. 兵器材料科学与工程, 2021, 44(5): 10.
[39] 何蕾 . Norsk Titanium 公司与 SAE 组织推出首项直接能量沉积增材制造技术相关规范[J]. 钛工业进展,2019, 36(2):47.
[40] 北京煜鼎增材制造研究院有限公司. 一种潜艇全钛耐压壳体及其增材制造装备和方法: CN202210014424[P]. 2022-02-08.
[41] 王逸尘 . 电子束熔丝沉积 TA15 合金组织演化规律和性能研究[D]. 哈尔滨:哈尔滨工业大学, 2021.
[42] 黄志涛, 锁红波, 巩水利,等 . TC18 钛合金电子束熔丝成形技术研究[J]. 航天制造技术, 2015(4): 14-17+21.
[43] SU B X, WANG B B, LUO L S, et al. Tuning micro⁃structure and improving the corrosion resistance of Ti-6Al-3Nb-2Zr-1Mo alloy the electron beam freeform fabri⁃cation [J]. Chemical Engineering Journal, 2022, 444:136524.
[44] XU J Q, ZHU J, FAN J K, et al. Microstructure and me⁃chanical properties of Ti-6Al-4V alloy fabricated using electron beam freeform fabrication [J]. Vacuum, 2019,167: 364-373.
[45] MANJUNATH A, ANANDAKRISHNAN V, RAMACH⁃ANDRA S, et al. Investigations on the effect of build ori⁃entation on the properties of wire electron beam additive manufactured Ti-6Al-4V alloy [J]. Materials Today Communications, 2022, 33: 104204.
[46] GOCKEL J, BEUTH J, TAMINGER K. Intergrated con⁃trol of solidification microstructure and melt pool dimen⁃sions in electron beam wire feed additive manufacturing of Ti-6Al-4V [J]. Additive Manufacturing. 2014 (1-4):119-126.
[47] ZHANG J H, YANG Y, CAO S, et al. Fine equiaxed β grains and superior tensile property in Ti-6Al-4V alloy deposited by coaxial electron beam wire feeding additive manufacturing [J]. Acta Metallurgica Sinica, 2022(33): 1311-1320.
[48] HU J N, ZHANG J H, WEI Y, et al. Effect of heat treat⁃ment on microstructure and tensile properties of Ti-6Al-4V alloy produced by coaxial electron beam wire feeding additive manufacturing [J]. Metals & Materials Society,2021, 73(7): 2241-2249.
[49] KALASHNIKOV K N, CHUMAEVSKII A V, KALASH⁃NIKOVA T A et al. A substrate material and thickness influence on the 3D-printing of Ti-6Al-4V components via wire-feed electron beam additive manufacturing [J].Journal of Materials Research and Technology, 2022,16: 840-852.
[50] 王晗 . 电子束熔丝沉积快速成形 Ti6Al4V-xB 合金的组 织 与 性 能 研 究[D]. 南 京 :南 京 航 空 航 天 大 学 ,2020.
[51] ZHANG D Y, QIU D, GIBSON M A, et al. Additive manufacturing of ultrafine-grained high-strength titani⁃um alloys [J]. Nature, 2019, 576(7785): 91-95.
[52] LI X S, YAO Z J, TAO X X, et al. Development Cu modified Ti6Al4V alloys with a combination of high strength and ductility by electron beam freedom fabrica⁃tion [J]. Vacuum, 2022, 194: 110638.
[53] 潘明财, 周杰, 郭顺, 等 . 钛/铜异种金属焊接微观组织及力学性能研究[J]. 铜业工程, 2023(2): 1-7.
[54] 靳文颖 . TC4钛合金电子束增材修复组织演变与力学性能分析[D]. 沈阳:沈阳航空航天大学, 2019.
[55] 王宁宁, 韩冬, 吴军, 等 . TC11 钛合金电子束熔丝增材复合制造工艺研究[J]. 航天制造技术, 2020(3):24-28.
[56] 王清江, 巩水利, 杨锐, 等 . 一种中强高韧性电子束熔丝堆积快速成形构件用钛合金丝材: CN102776412B[P]. 2016-04-27.
[57] 清江, 巩水利, 杨锐, 等 . 一种 920 MPa 强度级的电子束熔丝堆积快速成形构件用 α+β 型钛合金丝材:CN102888532B[P]. 2016-01-20.
[58] 刘建荣, 巩水利, 杨锐, 等 . 一种 960 MPa 强度级电子束熔丝堆积快速成形构件用 α+β 型钛合金丝材:CN102888531B[P]. 2016-01-20.
[59] 于卫新, 李士凯, 晏阳阳 . 一种 780 MPa 强度级电子束熔丝 3D 打印构件用钛合金丝材: CN106994471A[P]. 2017-08-01.
[60] 张国栋, 熊华平, 余槐, 等 . 一种用于电子束熔丝增材制造 TA15钛合金的丝材、制备方法: CN113878263A[P]. 2022-01-04.
[61] 江洪, 张晓丹 . 国外 3D 打印企业发展状况研究[J].新材料产业, 2017(1): 14-19.
[62] 王华明, 张述泉, 汤海波, 等 . 大型钛合金结构激光快速成形技术研究进展[J]. 航空精密制造技术,2008, 44(6): 28-30.
[63] 梁朝阳, 张安峰, 梁少端, 等 . 高性能钛合金激光增材制造技术的研究进展[J]. 应用激光, 2017, 37(3):452-458.
[64] MOK S H, BI G J, FOLKES J, et al. Deposition of Ti-6Al-4V using a high power diode laser and wire. Part I:investigation on the process characteristics [J]. Surface & Coating Technology, 2008, 202(16): 3933-3939.
[65] MOK S H, BI G J, FOLKES J, et al. Deposition of Ti-6Al-4V using a high power diode laser and wire. Part II:investigation on the mechanical properties [J]. Surface & Coating Technology, 2008, 202: 4613.
[66] BRANDL E, SCHOBERTH A, LEYENS C. Morpholo⁃gy, microstructure, and hardness of titanium (Ti-6Al-4V) blocks deposited by wire-feed additive layer manu⁃facturing (ALM) [J]. Materials Science and Engineer⁃ing A, 2012, 532(15): 295-307.
[67] 张大越, 刘旭明, 张建,等 . TC4-DT 激光熔丝增材制造微观组织与力学性能研究[J]. 钢铁钒钛, 2021, 42(6): 97.
[68] YUAN D, SHAO S Q, GUO C H, et al. Grain refining of Ti-6Al-4V alloy fabricated by laser and wire additive manufacturing assisted with ultrasonic vibration [J]. Ul⁃trasonics Sonochemistry, 2021,73(10): 105472.
[69] 严家印 . TC4钛合金激光熔丝增材制造工艺及组织性能研究[D]. 哈尔滨:哈尔滨工程大学, 2021.
[70] DING X P, MA H L, ZHANG Q, et al. Effect of anneal⁃ing heat treatment on microstructure and corrosion be⁃havior of Ti6Al4V alloy fabricated by multi-laser beam wire-feed additive manufacturing in vacuum environ⁃ment [J]. Journal of Alloys and Compounds, 2022(914): 914.
[71] KELBASSA J, GASSER A, BREMER J, et al. Equip⁃ment and process windows for laser metal deposition with coaxial wire feeding [J]. Journal of Laser Applica⁃tions, 2019, 31(2): 022320.
[72] 杜发瑞. 真空环境下钛合金激光熔丝增材制造成形工艺研究[D]. 重庆:重庆大学, 2019.
[73] SILZE F, SCHNICK M, SIZOVA I, et al. Laser metal deposition of Ti-6Al-4V with a direct diode laser set-up and coaxial material feed [J]. Procedia Manufacturing,2022, 47: 1154-1158.
[74] 武鹏博, 方乃文, 徐锴,等 . 一种 TC4钛合金低热输入高效激光熔丝增材制造方法: CN116652388A[P].2023-08-29.
[75] 方学伟, 李帛洋, 黄科, 等 . 一种激光同轴熔丝打印大型钛合金零件的装置及方法: CN112548115B[P].2023-03-31.
[76] 祁俊峰, 李敬洋, 潘宇新, 等 . 一种钛/铝异质合金摆动脉冲激光熔丝增材设备与方法: CN116117177A[P]. 2023-05-16
相关链接