引言
Ti6Al4V钛合金(TC4)具有强度高、耐高温、耐腐蚀等优点,能够满足工程上减重和增效的要求,被广泛应用于航空航天领域[1-3]。受其物理性能影响,钛合金是一种典型的难加工材料,一直以来都是国内外学者研究热点[4]。

金属切削去料加工的本质是刀刃与工件相互作用,被切削去料的工件发生弹性变形、塑性变形、断裂的过程[5]。在钛合金切削过程中,切削力是一个非常重要的物理量,它对刀具寿命、加工质量等都有显著影响,因此切削力的研究对提高刀具寿命,改善加工质量,提高加工效率具有非常重要的意义[6]。为此,国内外学者对钛合金去料加工开展了大量的研究。王雷[7]采用有限元分析方法结合ABAQus建立了钛合金切削仿真模型,并基于python语言通过二次开发建立了钛合金切削仿真参数化模型,主要是对主切削力的预测。战勇等[8]。建立了车削钛合金的仿真模型并进行了正交车削加工试验,得到车削加工钛合金时不同切削参数对切削力的影响规律。闫凯强等[9]。采用单因素实验法结合有限元仿真,探讨了在不同背吃刀量、铣削速度和进给量的条件下切削力的变化规律。邱旭[10]对超声振动钛合金三维微铣削加工过程进行了有限元仿 真,探究了超声振动对于钛合金微铣削加工过程中的切屑形成、切削力变化以及表面粗糙度的影响。
综上所述,国内外学者在探索TC4钛合金去料加工过程中的切削力及影响切削力规律做了研究,但对于TC4钛合金在3D铣削仿真状态下的以立铣刀刀尖切削力为观测点,探索不同加工工况下铣刀与工件在主分力、进给分力、背分力的分布情况却鲜有报道。本文基于ABAQus有限元仿真软件建立TC4钛合金在4刃等齿距立铣刀3D铣削仿真模型,结合实际加工工况设计在相同背吃刀量时以刀具角速度、进给速度为主要因素的正交仿真试验,揭示不同加工工况对主分力、进给分力、背分力的分布情况,以期为研究不同工况下TC4钛合金在铣削过程中切削力随时间的变化情况提供理论参考。
1、有限元仿真建模
在实际金属铣削中诸如机床动静刚度、加工工艺参数、刀具特性、冷却方式等均对铣削产生一定影响。金属铣削仿真属显式非线性动力学分析,在高度贴合实际铣削工况下建立简要的有限元模型,并提出如下几点假设:
(1)将刀具的进给速度、角速度作为输入载荷,为使在切削过程中保持直线切削,采取单一进给方向,且刀具在铣削过程中加速度为0m/s2;
(2)工件处于静态,采取在工件底部施加全约束即自由度为0;
(3)铣削过程连续,直至在工件表面铣削出完整的铣削槽;
(4)忽略铣削过程中因温度引起金相组织的变化,对TC4钛合金物理性能及化学成分不产生影响。
基于以上几点假设,利用solidworks建立了刀具三维模型导入ABAQus中建立刀具、工件有限元模型。在ABAQus仿真软件中,建立刀具与工件的装配关系,并对刀具和工件分别进行网格划分,网格划分质量直接影响有限元仿真分析的准确性,因刀具结构复图1工件和刀具有限元模型杂且不规则,故对刀具网格划分时采用四面体单元划分,工件结构简单采用六面体单元划分,为提高仿真精度及计算效率,对工件被铣削部分采取精细网格划分,未铣削部分采用粗略网格划分。刀具及工件所建有限元模型如图1所示。
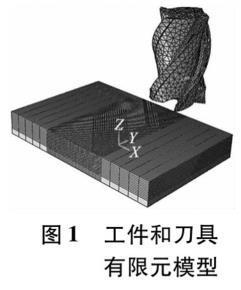
1.1刀具参数
加工钛合金时,普遍采用硬质合金刀具,根据加工经验通常使硬质合金刀具的切削速度限制在30~50m/min之间,即在这一铣削速度范围内研究铣削速度对TC4钛合金铣削的影响。本文旨在研究铣削参数对TC4钛合金铣削稳定性的影响,以solidworks建立了刀具三维模型,刀具参数表如表1所示。
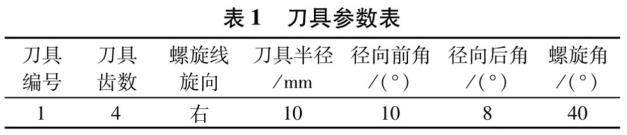
刀具材料为钨钴合金的硬质合金,属于YG类硬质合金,是常用的钛合金铣削加工刀具,其热力学性能如表2所示。
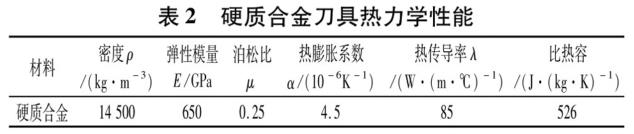
1.2材料的本构模型
仿真所用的工件材料为TC4钛合金具有良好的抗腐蚀性,性能优良。铣削加工仿真属于大变形分析,工件的本构关系模型选择典型的Johnson—cook本构模型其具体形式为[11]:

式中:A为准静态条件下的屈服强度,B为应变硬化参数,εp为等效塑性应变,n为硬化指数,C为应变率强化参数,ε量为等效塑性应变率,ε0为材料的参考应变率,T0为常温系数,通常取25℃;Tmelt为材料熔点,m为热软化参数。本次仿真采用的工件材料TC4钛合金Johnson—cook本构模型参数、损伤参数及物理性能如表3~表5所示。
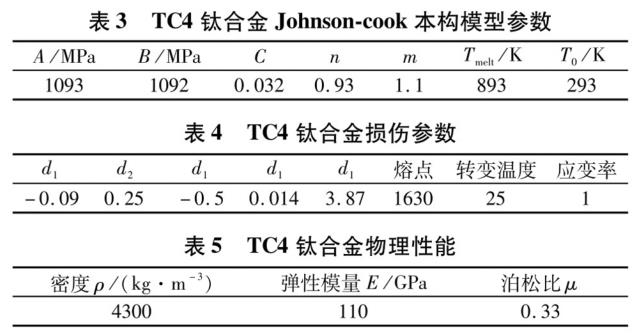
1.3铣削参数设计
合理的加工工艺路线和工艺参数对数控加工结果产生重要影响。根据实际加工为参照,以被铣削材料的物理性能,刀具的耐磨性、加工效率及使用寿命为依据,制定合理的背吃刀量、进给速度、铣削速度(角速度)。在ABAQus仿真软件中将刀具的进给速度和刀具角速度作为载荷输入,其中由主轴转速计算刀具角速度计算公式为:

式中:ω为刀具角速度(rad/min),n为主轴转速(r/min),按硬质合金刀具切削钛合金材料取经验值范围为
2500~3000 r/min。由此,ω的范围216~314 rad/s。
为得到合理的进给速度,根据进给速度计算公式:

式中f为每齿进给量,根据硬质合金刀具取经验值0.15mm/r;z为刀具齿数,本文设计刀具齿数为4;n为主轴转速经验值范围为2500~3000r/min。由此,Vf的范围为1500~1800mm/min。
1.4仿真试验方案设计
影响钛合金铣削稳定性因素主要有铣削速度、背吃刀量,进给速度。根据铣削参数设计作为参考,铣削速度范围为30~50 m/min,背吃刀量为0.3~0.75mm,进给速度范围为1500~1800mm/min,仿真试验中刀具铣削路径为单向直线,给出正交试验设计方案如表6所示。
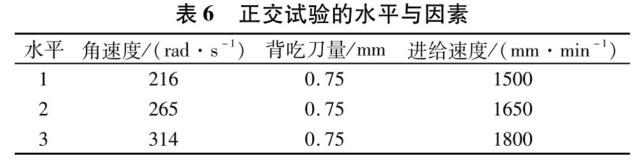
1.5位移边界条件
在工件底部边界施加全约束(自由度为0),刀具具有2个自由度,即绕刀具轴线方向的转动、沿走刀方向(y轴)的直线移动,为保证刀具沿固定方向移动,定义其在z轴、x轴速度为0,使之在移动过程中不发图2工件施加边界条件生偏移。
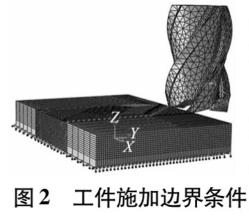
2、TC4钛合金铣削仿真
2.1铣削过程中整体应力
根据仿真工况表6在ABAQus软件中设置角速度、进给速度为载荷,将切削过程设置为200 fps,分别观察初段(50 fps)、中段(100fps、150 fps)、末端即(200 fps)时的应力状态,各阶段应力分布云如图3所示。由仿真结果得知,在0~50 fps段时在刀具铣削过程中,工况l产生的切削应力较大约为3.29×103MPa,而切削过程中应力较小的为工况2,其值为2.95×103 MPa,即在铣削初段刀具的进给速度、角速度越小产生的切削应力反而更大。当切削进行至中段,最大切削应力均为工况2,其值分别为3.47×103MPa、3.55×103 MPa,3种工况在中段切削应力其值较小且较为稳定为工况1,分别为2.98×103 MPa、3.06×103MPa,对比工况1与工况3,两者在中段的切削应力相差较小,从加工效率角度分析,工况3既能保持相对较低的铣削应力又具备较好的铣削效率。当刀具铣削出完整铣削槽即切削过程进行至末端,工况2在3种工况下的铣削应力值最大,最大应力值为3.25×103MPa,最小应力值为工况3时3.01×103MPa,此时工况3作为TC4钛合金铣削加工参数较为合理。综合以上分析结果,工况l在铣削初段时产生的切削应力较大,铣削中段及末段时工况2产生的切削应力较大,由此可知将工况3作为TC4钛合金铣削加工参数时其切削应力较小,具有较好的铣削稳定性。
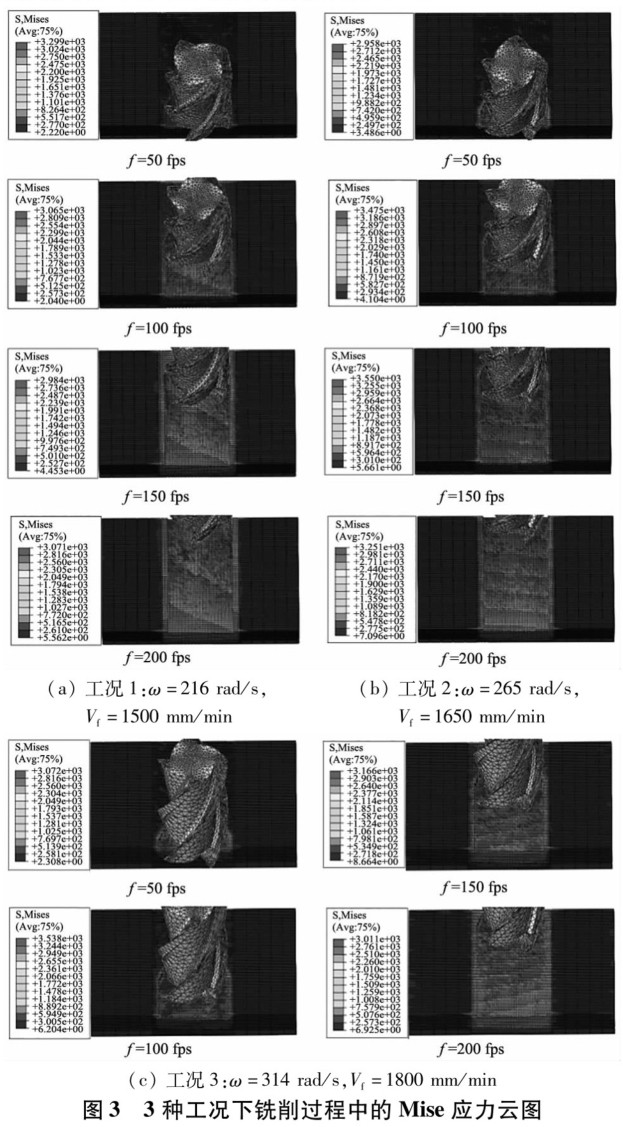
2.2铣削过程中的切削力
铣削过程刀具与工件因去料产生相互作用的切削力,立铣刀铣削过程中产生的切削力如图4所示,z轴为主轴方向,刀具进给速度沿y轴正向。基于ABAQus三维铣削仿真,选取四刃立铣刀中其中一刃刀尖作为观察切削力变化的参考点,因刀具自身角速度与进给速度使选取的刀尖参考点与工件之问产生连续随时问变化的切削力曲线。
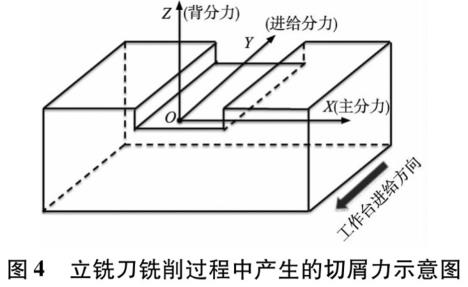
2.2.1不同工况下x轴向切削力分析
当刀具在主轴转速作用下,在与旋转相反方向上产生的作用力为主分力即沿x轴方向,此力决定主轴所需功率大小且影响刀具在铣削过程中产生的热量,x轴切削力作为主分力对铣削稳定性具有重要影响。
根据3种不同工况分别由ABAQus软件导出x轴方向的切削力(主分力)随时问变化曲线如图5所示。从图5中3种工况下的切削力随时问变化曲线可知,X轴方向切削力随刀具的角速度和进给速度越大其产生的切削力亦越大。
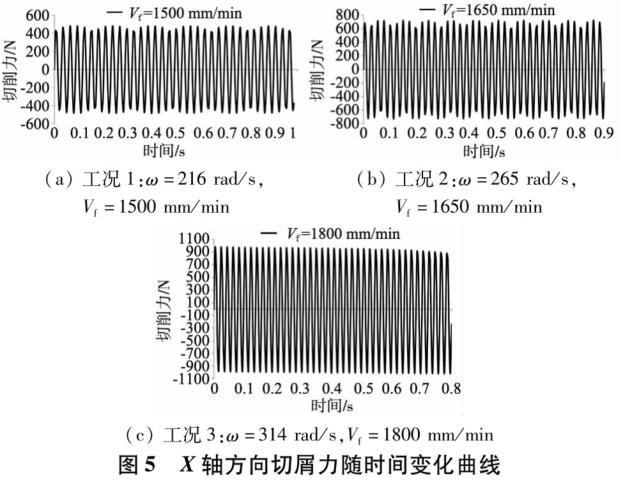
为观测X轴切削力在正负极值的波动幅度以反映在极值时切削力稳定性,文本于表7中分别列出了3种工况下X轴切削力的正负极值平均值、正极值方差和负极值方差。因3种工况下正负极值的平均值不同,存在一定差异,故方差的大小不能完全反映正负极值波动性,此时引入变异系数即方差与平均值比值。由表7中的正负变异系数可知,工况3的正负极值变异系数最小分别为2.63%、1.31%,而工况2正负极值变异系数最大分别为5.43%、5.60%。综合图5中不同工况下x轴切削力变化曲线及表7中正负极值变异系数可知,当采用工况3作为铣削加工参数时,铣削稳定性较好。
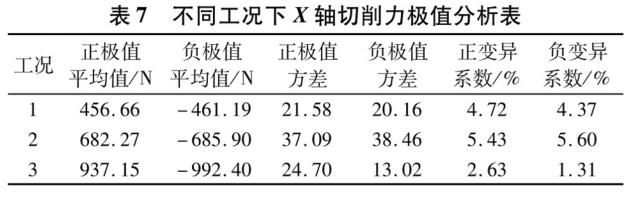
2.2.2不同工况下Y轴向切削力分析
当刀具在进给速度作用下沿Y轴正向移动时产生的相互作用力为进给分力,此力使刀具实际主轴线发生偏移,与理论刀具轴线形成夹角,即实际铣削面与理论铣削面成一定角度。因此进给分力主要影响铣削面的加工精度,故l,轴切削力对铣削稳定性产生重要影响。在3种工况下y轴切削力随时间变化曲线如图6所示,当刀具转速和进给速度越大其产生的切削力越大,在工况1和工况2时,Y轴切削力虽较小,但在正极值和负极值呈现一定波动,而在工况3时切削力最大单正极值和负极值波动相对较小。
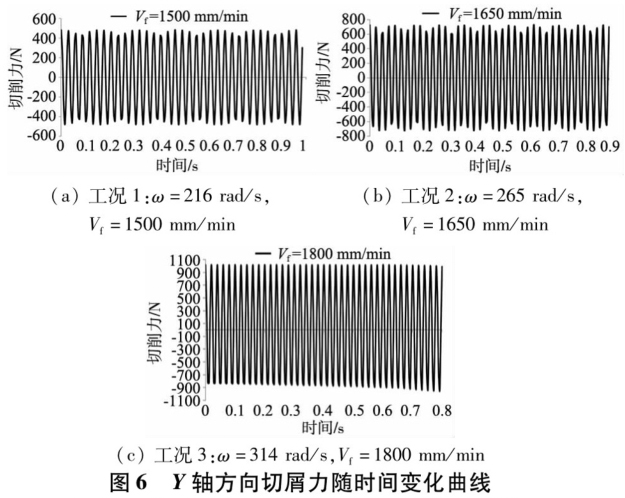
为观测Y轴切削力在正负极值的波动幅度以反映在极值时切削力稳定性,从ABAQus导出图6中切削力正负极值数据并求其平均值、方差及变异系数于表8。由表8中的正负变异系数可知,工况3的正负极值变异系数最小分别为0.63%、3.64%,而工况2正负极值变异系数最大分别为5.48%、5.69%。综合图6中不同工况下Y轴切削力变化曲线及表8中正负极值变异系数可知,当采用工况3作为铣削加工参数时,铣削稳定性较好,但相较于工况1、2,其切削力过大时易影响刀具使用寿命和加工精度。
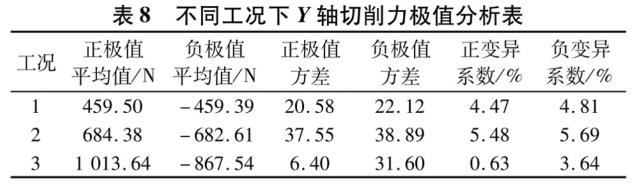
2.2.3不同工况下Z轴向切削力分析
当刀具在铣削过程中与工件相互作用时Z轴产生的相互作用力为背分力,此时刀具受力情况可视为一端固定、一端属于自由端的悬臂梁力学模型,从受力分析得出刀具自身会发生挠曲变形,主要影响铣削加工尺寸,故Z轴切削力对铣削稳定性产生重要影响。此外,本文在仿真工况中设置约束为工件底部即Z轴为工件底部的法线方向,故Z轴切削力亦能反映铣削过程中刀具与工件间振动。
在3种工况下Z轴切削力随切削时间变化曲线如图7所示,3种工况下Z轴切削力在0~10 N范围内波动,由图7可知,从工况1至工况3下Z轴切削力的极值个数分别为5个、6个、9个,且在铣削过程中Z轴切削力均出现突变式波动,Z轴最大切削力为工况2下的9.15 N,工况3下的最大切削力为7.64 N,小于另外两种工况的最大切削力。总体上分析Z轴切削力发现,工况l的z轴切削力最大值为8.36 N,平均值为2.44 N,工况2下的z轴切削力平均值最小为2.18N。为能客观地反映3种工况下z轴切削力的波动幅度考虑其切削力方差分别为1.95、1.91、1.89。由方差值结果表明,工况3下的z轴切削力稳定性较好。
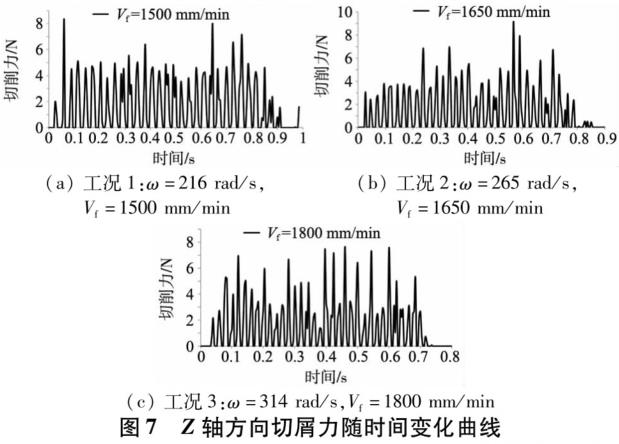
3、结论
基于ABAQus有限元软件建立硬质合金刀具铣削TC4钛合金三维铣削模型,根据实际加工情况设立约束条件,以刀具的进给速度和角速度作为输入载荷探讨不同工况下TC4钛合金铣削过程中切削力随时问的变化情况。
(1)将铣削过程设置为200 fps,每50 fps作为一个观测段,本文将0~50 fps定义为初段,50~100 fps、100~150 fps均作为中段观测段,150~200 fps为末端观测段,根据仿真结果得知,工况1在初段的切削应力较大,中段切削应力其值较大为工况2,当刀具铣削出完整铣削槽即切削过程进行至末端,当铣削参数为工况3时切削应力最小。综合仿真结果分析可知,将工况3作为铣削加工参数易获得稳定铣削性能。
(2)在3种工况下分析刀具与工件之间相互作用力,从主分力、背分力、进给分力分析了铣削过程中切削力随时间的变化规律,将主分力作为观察因素时发现,工况3下切削力最大但正负极值变异系数最小分别为2.63%、1.31%,即铣削过程中铣削稳定性较好。若将进给分力作为切削力稳定性参考因素,工况3虽正负变异系数最小,但出现切削力的正负极值平均值相差较大,使刀具受力不均影响刀具使用寿命和加工精度,而工况2的正负极值平均值相近,正负变异系数与工况1相近,此时工况2可作为较理想的铣削加工参数。从仿真结果来看,背分力值远小于主分力、进给分力值,背分力值在0~10 N范围内波动,综合3种铣削工况仿真结果,工况3既能实现切削力的稳定性又能提高铣削加工效率。
[参考文献]
[1]王长清,张毅飞,郑勇,等.钛合金薄壁件切削力与残余应力研究[J].重庆理工大学学报,2022,36(3):95—104.
[2]CHANG P L.Processing mechanism of electricaI dischage—assisted milling titanium alloy based on 3 D thermal—mechani—cal coupling cutting model[J].Joumal of Manufacturing Processes,2022,78:107一119.
[3]xuE s H,DING z H,cHANG Y F,eta1.Research onpa— rameter identification of Johnson—Cook constitu“ve model for TC17 titanium alloy cutting simulation[J].Materials Today Communications.2022.31:18—30.
[4]王荣华,汪振华.TC4钛合金铣削力及表面粗糙度分析[J].工具技术,2021,55(5):30—33.
[5]刘英,袁绩乾.机械制造技术基础[M].北京:机械工业出版社,2008.
[6]续文浩.钛合金叶片型面铣削工艺优化试验与应用研究[D].上海:上海交通大学,2019.
[7]王雷.基于BP神经网络的钛合金加工切削力预测模型研究[D].天津:天津理工大学,2016.
[8]战勇,金成哲,张莹莹.切削参数对车削钛合金切削力影响的研究[J].工具技术,2021,55(10):23—27.
[9]闫凯强,黄晓斌,张仕杰,等.面铣刀铣削钛合金时切削参数对切削力影响规律的仿真[J].工具技术,2022,56(4):80—83.
[10]邱旭.TC4钛合金超声振动辅助微铣削加工装置研制及工艺研究[D].哈尔滨:哈尔滨工业大学,2021.
[11]NING J,LIANG S Y.Model一driven determination of John—son—Cook material constants using temperature and fbrce measurements[J].International Journal of Advance Manu—facturing Technology,2018,97:1053—1060.
相关链接